Table of Content
1 What Is a Quality Management System (QMS)?
Key components that are often part of a QMS include:
3 Benefits of a Quality Management System
Common Types of Quality Management Systems
5 How to Implement a Quality Management System
Common Pitfalls to Avoid in QMS Implementation
Why Choose Qualityze EQMS?
8 Conclusion
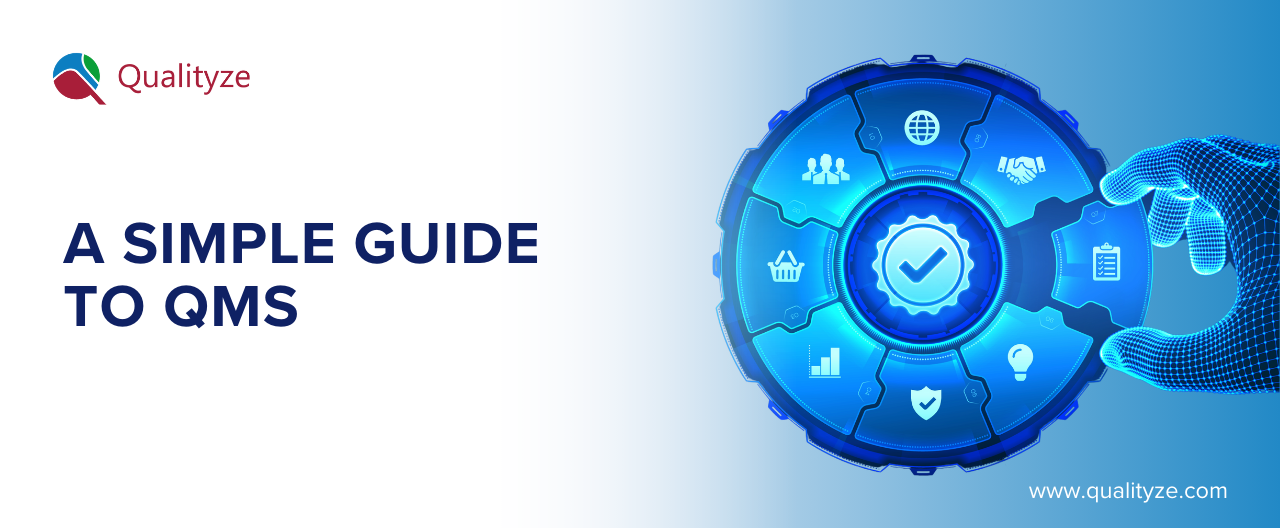
Quality is how well something meets its intended purpose and satisfies customer expectations. In simple terms, a product or service is "quality" if it does what it’s supposed to do and the customer is happy with it.
Quality could mean slightly different things in different industries, but it always comes down to meeting certain standards or requirements. If a product meets all the set specifications and standards, we consider it to have high quality. Usually, the more a product conforms to the requirements (for example, design specifications or safety rules), the more reliable and trustworthy it is. High conformance leads to high reliability and customer trust.
What Is a Quality Management System (QMS)?
A Quality Management System (QMS) is a set of processes, policies, and procedures that a company follows to ensure quality in everything it does. It is essentially a framework that guides how a business manages quality so that its products or services consistently meet requirements and expectations . It documents who does what, how, and when to maintain quality. This includes guidelines for processes, standards to follow, and responsibilities of team members.
By following the QMS, everyone in the organization knows how to do their job the right way to avoid mistakes and satisfy customers.
Key components that are often part of a QMS include:
- Policies and Objectives: The company’s quality policy (a statement of commitment to quality) and specific goals for quality improvement.
- Standard Processes and Procedures: Step-by-step instructions for critical tasks (often called Standard Operating Procedures or SOPs) to ensure each task is done correctly and the same way each time.
- Documentation and Records: Controlled documents that record processes and changes, and records that show outcomes (e.g., inspection reports, test results, training logs). Keeping documents organized and up-to-date is essential for consistency and for audits
- Roles and Responsibilities: Clear assignment of who is responsible for which quality-related tasks (for example, managers, team leaders, quality control inspectors, etc.).
- Training Programs: Plans to train employees so that everyone knows how to do their job according to the QMS and is aware of the importance of quality .
- Feedback and Improvement Processes: Methods to collect feedback (like customer complaints or internal audits) and improve processes based on that feedback. This ensures continuous improvement, meaning the company keeps finding ways to do things better over time.
- Audit and Review Schedules: Regular checks (internal audits) to make sure the procedures are followed and effective. Management also reviews the QMS periodically to decide on improvements.
In summary, a QMS is the way an organization directs and controls quality. It helps coordinate activities so that the company can meet customer needs, comply with regulations, and continually improve its efficiency and effectiveness . With a good QMS, quality is not left to chance; it is planned, monitored, and improved in a systematic way.
Benefits of a Quality Management System
Implementing a Quality Management System brings many benefits to an organization. Here are some key advantages:
- Consistent Quality and Fewer Defects: When processes are followed, there are fewer errors and defects in products.
- Increased Efficiency and Lower Costs: Leaner processes require less effort and resources to produce the same output. Over time, this can significantly lower operating costs for the business.
- Compliance with Regulations and Standards: Many industries have regulations (safety laws, environmental rules, etc.) or standards (like ISO 9001 for quality, ISO 13485 for medical devices, or ISO 22000 for food safety) that companies must follow. It helps avoids legal problems, fines, or recalls and helps in obtaining and maintaining certifications that boost the company’s reputation and trustworthiness.
- Better Customer Satisfaction: When quality is consistent and high, customers are happier. Happy customers are more likely to be repeat customers and recommend the business to others.
- Clear Processes and Employee Confidence: Well-documented processes and proper training (which are part of the QMS) give employees confidence that they are doing things correctly. When employees know the right way to do their work, it prevents misunderstandings and helps operations run smoothly. Engaged and confident employees often have higher morale and are more productive.
- Continuous Improvement Culture: A QMS isn’t a one-time setup – it encourages continuous improvement. This means the company constantly looks for ways to do better, whether it’s through regular audits, feedback collection, or improvement projects. Over time, this culture of improvement can lead to innovation, better methods, and staying ahead of competitors. It also makes the company more adaptable to changes. *
- Better Decision Making with Data: A good QMS involves keeping records of performance (like defect rates, audit results, customer complaints). By analyzing this data, management can make informed decisions. Instead of guessing what might be wrong, they can pinpoint problem areas.
- Improved Supplier Quality and Relationships: Quality management extends to supplier quality as well. Many QMS frameworks include evaluating and monitoring suppliers to ensure they provide quality materials or components. By working closely with suppliers under clear requirements, a company can prevent quality issues at the source. This leads to more reliable supply chains and often better relationships with suppliers.
- Enhanced Customer and Market Trust: Being able to demonstrate a strong QMS (especially if certified to a standard like ISO 9001) can enhance a company’s reputation. It signals to customers and partners that the company is serious about quality. This trust can be critical for winning contracts, especially in sectors where quality and safety are paramount.
In short, a QMS helps a business do things right the first time and consistently. This leads to cost savings, happy customers, engaged employees, and a smoother operation overall . It aligns the entire organization towards delivering quality, which ultimately drives success and profitability.
Common Types of Quality Management Systems
There are several established frameworks and standards that organizations use as a model for their Quality Management System. These frameworks provide guidelines and best practices that can be adapted to different businesses. Here are some of the most common ones:
- ISO 9001: This is the most widely used QMS standard in the world. ISO 9001 provides a set of requirements for a quality management system, focusing on meeting customer requirements, following defined processes, managing risks, and striving for continuous improvement. Companies in many industries (manufacturing, services, construction, etc.) pursue ISO 9001 certification to demonstrate that their QMS meets international standards.
- ISO 9000 Series: The ISO 9000 family includes ISO 9001 (which has requirements to follow) and other standards like ISO 9000 (which covers basic concepts and vocabulary of quality management) and ISO 9004 (guidelines for performance improvements beyond the basics). Often when people say "ISO 9000 certified," they mean ISO 9001 certified, since ISO 9001 is the actual certifiable standard.
- Industry-Specific QMS Standards: Different industries have their own specialized QMS standards derived from ISO 9001 but with additional requirements for that sector:
- Automotive (IATF 16949): This is a QMS standard for the automotive industry. It includes specific requirements for car manufacturers and parts suppliers, emphasizing defect prevention and variation reduction in the auto supply chain.
- Aerospace (AS9100): This standard is used in aerospace and defense manufacturing. It adds requirements for areas like configuration management, product safety, and risk management due to the high stakes in aerospace.
- Medical Devices (ISO 13485): A QMS standard focusing on medical device companies. It ensures that medical products are safe and effective by requiring risk management, sterile manufacturing processes, and regulatory compliance throughout product lifecycles.
- Food Safety (ISO 22000): This standard is for food production and packaging companies. It combines general QMS principles with food safety management (HACCP principles).
- Information Technology (ISO 27001): While ISO 27001 is primarily an information security management standard, it is sometimes considered alongside quality for IT service organizations. It ensures quality in managing information security processes.
- General Industry (Total Quality Management - TQM): TQM is not a formal standard like ISO, but rather a holistic approach or philosophy. It gained popularity as a way to involve the entire organization (from CEO to front-line workers) in continuous improvement. The idea is that quality is everyone’s responsibility and improving quality is a continuous process, not just a one-time goal.
- Six Sigma: Six Sigma is a methodology aimed at reducing defects and variability in processes. It uses data and statistical analysis to find the causes of defects and eliminate them. Companies often use Six Sigma alongside their QMS to tackle specific quality improvement projects.
- Lean Manufacturing: Lean focuses on eliminating waste (such as excess inventory, waiting time, unnecessary motions) to improve efficiency. While originally developed for manufacturing, its principles apply to many environments. Lean and quality go hand-in-hand, as removing waste often also improves quality (fewer chances for error, simpler processes).
These frameworks and approaches often overlap or are used together. Many companies adopt ISO 9001 as a baseline QMS framework, then add industry-specific standards or methodologies (like Six Sigma or Lean) on top of it for further improvement. The choice of framework depends on the company’s needs, the industry requirements, and customer expectations. But regardless of the framework, the core goal remains the same: establish a system that ensures quality is built into every part of the operation.
Tip: If you are new to QMS, ISO 9001 is a good starting point because it’s generic and flexible. Once the basic system is in place, you can tailor it or integrate other methods as needed.
How to Implement a Quality Management System
Implementing a QMS in an organization is a step-by-step process. It requires careful planning, commitment from leadership, and involvement of employees at all levels. Below is a straightforward roadmap with steps to set up a QMS and get it working effectively:
- Obtain Management Commitment: Start at the top. Senior management must fully support the QMS initiative. Without leadership buy-in, a QMS will fail because it touches all parts of the organization.
- Build a QMS Implementation Team: Designate a dedicated team to plan and roll out the QMS. This team should include people from different departments (production, maintenance, sales, customer service, etc.) to make sure the QMS covers the whole organization.
- Identify Requirements and Goals: Before designing new processes, assess what requirements you need to meet. These include:
- Customer Requirements: What do your customers expect in terms of quality? (e.g., product performance, on-time delivery, service response time).
- Internal Requirements: What internal standards or goals does the company have? (e.g., reduce defect rate by 10%, improve production speed, ensure safety protocols are met).
- External Requirements: What laws, regulations, or industry standards apply? (e.g., safety regulations, environmental laws, industry-specific standards like ISO or FDA requirements for medical or food companies).
A clear understanding of these requirements will shape your QMS.
- Analyze Current Processes (Gap Analysis): Review your organization’s current processes and compare them against the identified requirements and best practices (often called a gap analysis) . Document what you currently do for each major activity – how do you design products, how do you train staff, how do you handle customer complaints, etc. Then see what’s missing or not up to standard. This analysis will highlight what new processes or changes you need for the QMS. (This step is like checking the map before a journey – you figure out where you are now and what the distance is to where you need to be.)
- Design and Document the QMS Processes: Based on the gaps identified, create the processes and procedures required for the QMS. Start writing down the procedures in a clear, step-by-step format. Each procedure should have a purpose, scope, and responsibilities defined. Good documentation is crucial: “If it’s not documented, it’s not done” is a common saying in quality management. So, document what needs to be done, and also what has been done (through records). Use simple language and, if possible, visual aids (flowcharts or diagrams) to make procedures easy to understand for everyone.
- Provide Training and Awareness: A QMS can only work if people know about it and understand it. Conduct training sessions for all employees to explain the new processes, their roles in the QMS, and why it’s important . Make it practical by including examples relevant to their daily work. Also, encourage employees to ask questions and provide feedback during training. An informed and engaged workforce will follow the QMS more willingly and effectively.
- Implement the Processes and the QMS Infrastructure: Now, put the documented processes into action. This might be done department by department or process by process. It could help to do a trial run (or pilot) in one area to work out any kinks before rolling out company wide. Ensure that all the necessary tools or systems are in place.
- Document and Control Records: As processes run, they will generate records (such as inspection logs, training attendance, audit findings, etc.). Establish a document control system to manage both the QMS documentation and the records. This usually means deciding where these documents and records will be stored (physically in a file room, or digitally on a server or cloud), who can access them, and how to ensure they are updated properly.
- Conduct Internal Audits: Once the QMS is in place and running for a while, you need to verify that it is effective. This is done through internal audits – basically, self-checks. Trained internal auditors (who could be employees from a different department or designated quality staff) will review processes and records to see if people are following the QMS and if the QMS is achieving its goals. The findings of internal audits tell you where the QMS might not be working as intended. Perhaps a certain procedure is often skipped or misunderstood – that needs attention. Schedule internal audits regularly (e.g., every 6 months or annually, depending on your company’s size and risk) and cover all areas of the QMS over time.
- Review Results and Take Corrective Actions: After audits (or any time you find an issue, such as a customer complaint or a process error), use the QMS’s corrective action process to fix the root cause of problems. This means not just fixing the immediate issue, but figuring out why it happened and preventing it from happening again. Management should also hold regular management review meetings (commonly done annually or semi-annually) to look at the big picture of the QMS: audit results, customer feedback, key performance metrics (like defect rates, on-time delivery, etc.), and decide on improvements or resource needs. This is where the QMS becomes a cycle of continuous improvement – you check how it’s working, make adjustments, and then continue running the improved processes.
- Seek Certification (Optional): If your goal is to get certified to a standard like ISO 9001, the final step is to invite an external certification body to conduct an audit. They will assess if your QMS meets all the requirements of the standard. If you’ve followed the steps above diligently, you should be ready. Upon passing, you get a certificate that is usually valid for three years (with minor surveillance audits in between). Certification can be a great achievement, but remember, the true aim of the QMS is improving your business, not just getting a certificate. Many small businesses implement QMS practices without formally certifying, and they still reap the benefits of better organization and quality.
- Maintain and Improve the QMS: Implementation is not a one-and-done project. It’s an ongoing effort. Keep the QMS alive by updating documents when processes change, continuously training new employees or refreshing training for existing staff, and always looking for improvement opportunities. The motto should be “Plan – Do – Check – Act” (the PDCA cycle) on repeat: Plan what you need to do (set processes and goals), Do the work as planned, Check the results (through audits and metrics), and Act on findings to make things better. This cycle ensures that quality management becomes part of the company’s culture.
By following these steps, even a company new to formal quality management can set up a QMS that is effective. The key is that the QMS should work for you (and not be just paperwork). When properly implemented, a QMS becomes simply “how we do things here” – which means doing things the right way, every time.
Common Pitfalls to Avoid in QMS Implementation
While implementing a QMS brings many benefits, there are also common challenges and mistakes to watch out for. Being aware of these pitfalls can help you avoid them:
- Lack of True Management Support: Ensure leaders are visibly committed – for instance, attending training, mentioning quality in meetings, and considering quality metrics in evaluations.
- Treating QMS as a Paperwork Exercise: Keep the QMS practical. Involve the people who do the work in writing procedures so that the documents match reality. Update the documents when things change. Use the QMS as a tool to help work, not as an obstacle.
- Poor Employee Engagement and Training: Invest time in training and communication. Explain the “what’s in it for me” – for example, how a QMS makes jobs easier or more secure (fewer crises or fire-fighting when quality is under control). Encourage questions and feedback from staff to get their buy-in.
- Overcomplicating the System: Aim for simplicity. Keep procedures concise. Don’t document trivial things that don’t impact quality. Use clear language (avoid jargon) and make the system user-friendly. The simpler the system, the more likely everyone will follow it.
- Ignoring Company Culture: Work with the culture. Use influencers within the company to promote the QMS. If the culture values teamwork, frame the QMS as a team effort to improve. If it values innovation, emphasize how quality improvement is a form of innovation in processes.
- Not Using Data for Improvement: Use the data your QMS generates. Analyze trends – are defects going down? What types of complaints are most common? Hold regular discussions on this data and prioritize improvement projects. Also, when a problem is found, use techniques like root cause analysis (asking “why?” multiple times) to find the real cause and fix it, rather than just the symptom.
- Infrequent or Superficial Audits: Schedule audits at a reasonable frequency and ensure auditors are objective (having someone audit their own work is not effective – get cross-department participation). Take audit findings seriously – they are opportunities to improve.
- Failure to Update the QMS: Whenever there’s a significant change in the business, ask “Does our QMS documentation need to change too?” Have a process for document change control and make it known that updating processes is a normal part of the QMS lifecycle. Encouraging feedback will help catch when something in the QMS isn’t working well so it can be revised.
By avoiding these pitfalls, you can ensure that your QMS implementation is not only smooth but also sustained.
Why Choose Qualityze EQMS?
Setting up a QMS can feel like a lot. That’s where Qualityze comes in. It’s a modern system built to make quality simple.
Here’s what Qualityze offers:
- Pre-Configured Workflows – Use proven methods right away.
- AI Assistant (QAI) – Smart suggestions help you make better decisions.
- Easy Interface – Simple enough for anyone to use.
- Works With Other Tools – Links to ERP, CRM, and more.
- Real-Time Dashboards – Always know what’s working and what’s not.
Qualityze turns your QMS into a business tool—not just a way to check boxes.
How a QMS Helps Quality Leaders
If you're in charge of quality, a QMS gives you the tools to lead well.
It helps you:
- See Everything – Track quality across the whole company.
- Work as One Team – Get departments talking and working together.
- Make Smart Choices – Trust your data, not just your gut.
- Save Time – Focus on improvements instead of fixing the same problems.
- Involve the Team – Help others take ownership of quality.
Qualityze goes further with tools like smart dashboards and flexible setups. You can lead with more confidence and less stress.
Conclusion
By focusing on quality – doing things right and improving them over time – companies large and small can achieve greater customer satisfaction, lower costs, and a stronger reputation. A QMS like Qualityze provides the structure and discipline to make quality a natural part of everyday work.
It ensures that you, “Say what you do, do what you say, and improve along the way.” See it in action today by requesting a personalized demo.
Remember: quality is a journey, not a destination. With a good QMS, you’re well-equipped to travel that journey successfully.
Share
The Start of Something Amazing.
Request Demo
Products
Industries