Table of Content
1 What is a US FDA Quality Plan?
Why Does It Matter?
3 Essential Elements of a US FDA Quality Plan
Management Responsibility: Leadership Drives Quality
Risk Management & CAPA (Corrective & Preventive Actions)
Document & Record Control: The Compliance Lifeline
Supplier & Vendor Management: Quality Beyond Your Walls
Product & Process Control: Quality at Every Stage
Complaint Handling & Post-Market Surveillance
10 US FDA Quality Plan Guidelines: What You Need to Know
FDA Quality System Regulation (QSR) – 21 CFR Part 820
21 CFR Part 11 – Electronic Records & Signatures
ISO 13485 – The Global Medical Device QMS Standard
FDA’s Risk-Based Approach to Compliance
15 Steps to Create a US FDA Device Quality Plan
Step 1: Assess Regulatory Requirements Specific to Your Industry
Step 2: Define Your Quality Objectives & Key Performance Indicators (KPIs)
Step 3: Establish Documentation & Recordkeeping Procedures
Step 4: Implement a Risk-Based CAPA & Change Management System
Step 5: Build a Supplier & Vendor Compliance Program
Step 6: Ensure Employee Training & Compliance Awareness
Step 7: Implement Audit-Ready Monitoring & Continuous Improvement
23 Crafting an Effective US FDA Quality Plan with Qualityze
1. Centralized Secure Cloud Platform
2. Fully Integrated CAPA & Change Management
3. Automated Supplier Quality Management
4. Streamlined Training & Compliance Awareness
5. Real-Time Audit Management & Continuous Improvement
6. Post-Market Surveillance & Complaint Management
30 Final Thoughts
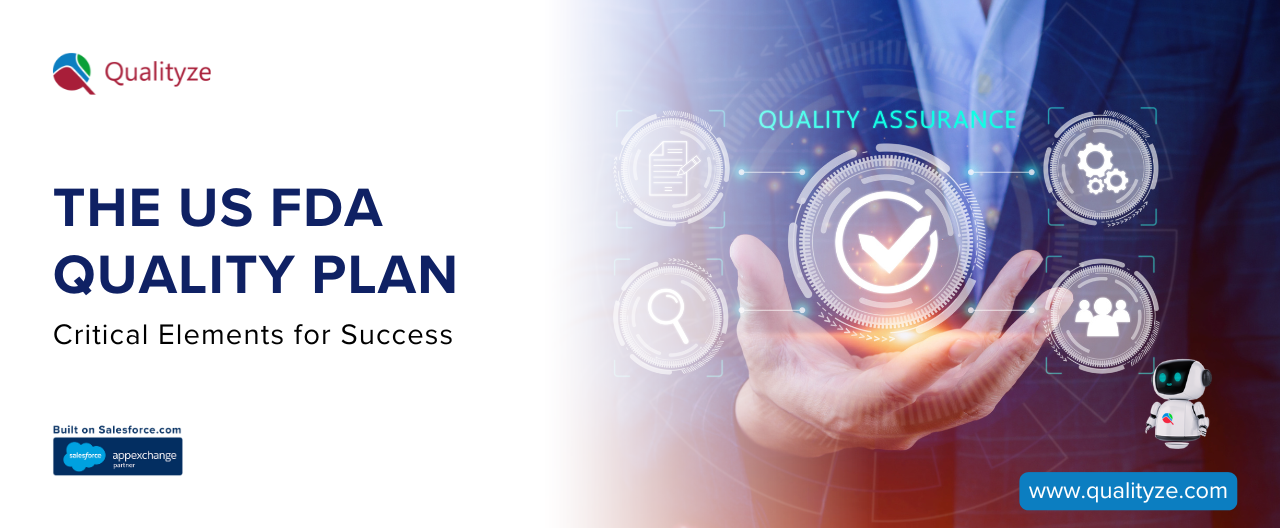
Let’s talk about Compliance. No, not the dull, paperwork-heavy, “check-the-box” kind of Compliance. We mean absolute Compliance—preventing warning letters, recalls, and million-dollar penalties while making your operations smoother, faster, and more efficient.
If you are in a regulated industry—medical devices, pharmaceuticals, biotechnology, or even food manufacturing—you know how strict FDA standards are. Failing to meet quality standards isn’t just a minor inconvenience; it’s a business risk. One recall or a non-compliance penalty could mean lost customers, tarnished reputation, and costly fixes.
That’s where a US FDA Quality Plan comes in. Think of it as your company’s quality playbook—a structured approach to ensuring every process, product, and document meets regulatory standards. When done right, it doesn’t just help you “pass audits”—it enables you to create better products, improve operational efficiency, and scale confidently.
So, what makes a strong FDA Quality Plan? What are the must-have elements that keep you ahead of compliance issues? More importantly, how can you make your quality plan work for you rather than make it feel like a bureaucratic burden?
We’ll cover all that in this blog, but before we dive in, let’s answer the biggest question first:
What is a US FDA Quality Plan?
A US FDA Quality Plan is a master blueprint to ensure that your products meet FDA regulations and industry standards. It is a strategic framework that aligns your operations with compliance requirements while keeping quality at the core.
Think of it like a GPS for quality and Compliance—helping you navigate complex regulations, avoid costly detours (like FDA warning letters and recalls), and reach your ultimate destination: a fully compliant, high-quality product that wins customer trust and regulatory approval.
Why Does It Matter?
If you’re manufacturing medical devices, pharmaceuticals, or other FDA-regulated products, an FDA-compliant Quality Plan isn’t optional—it’s mandatory. Without one, you’re setting yourself up for compliance risks, inefficient processes, and potential regulatory actions that could halt your business.
A well-structured FDA Quality Plan ensures that:
- Your processes are aligned with FDA regulations (like 21 CFR Part 820 for medical devices and 21 CFR Part 211 for pharmaceuticals).
- Every stage of your product lifecycle—design, production, inspection, and post-market monitoring—meets strict quality requirements.
- You have a proactive system to detect, correct, and prevent quality issues before they escalate.
- Your team knows precisely what to do, how to do it, and when to do it, eliminating guesswork and inconsistencies.
In short, an FDA Quality Plan is the backbone of a successful, compliant business. It’s what separates companies that thrive in regulated markets from those that struggle with audits, product failures, and costly delays.
But what exactly does an effective FDA Quality Plan include?
Essential Elements of a US FDA Quality Plan
Management Responsibility: Leadership Drives Quality
Quality is more than just a department—it’s a culture that starts at the top. The FDA expects executive management to actively participate in quality planning, reviews, and continuous improvement.
Your plan should outline:
✔ Roles and responsibilities of leadership in maintaining quality.
✔ A structured Management Review process to track quality trends and address risks.
✔ Commitment to providing the required resources and training for Compliance.
Risk Management & CAPA (Corrective & Preventive Actions)
A good FDA Quality Plan is proactive, not reactive. It should include a structured approach to identify, assess, and mitigate risks before they lead to serious compliance violations.
Key components:
✔ Risk-based decision-making following ISO 14971 for medical devices.
✔ A well-documented CAPA process that ensures quality issues are investigated and resolved correctly.
✔ Procedures for detecting trends in non-conformance and complaints before they escalate.
Fun Fact: 48% of FDA warning letters cite CAPA deficiencies. Don’t be part of that statistic!
Document & Record Control: The Compliance Lifeline
If it’s not documented, it didn’t happen—at least in the FDA’s eyes. Your FDA Quality Plan must outline how you handle documentation and record-keeping to meet compliance requirements.
Essential points:
✔ Compliance with 21 CFR Part 11 for managing electronic records and signatures.
✔ Version control and access restrictions to ensure document integrity.
✔ Procedures for audit trails, approvals, and data retention policies.
Bonus Tip: A cloud-based document management system (like Qualityze) can automate version control, approvals, and audit trails to keep you FDA-ready 24/7.
Supplier & Vendor Management: Quality Beyond Your Walls
Your product is only as good as the materials and services you rely on. The FDA expects companies to have a rigorous supplier qualification and monitoring process.
Your plan should cover:
✔ Supplier qualification and approval processes.
✔ Regular supplier audits and performance monitoring.
✔ Procedures for managing non-conforming supplier materials.
Product & Process Control: Quality at Every Stage
Your FDA Quality Plan must ensure that products are consistently manufactured to meet specifications. This means controlling every design, production, testing, and inspection aspect.
Key areas:
✔ Design controls (especially for medical devices per 21 CFR Part 820.30).
✔ Process validation and production control to maintain consistency.
✔ Change management procedures to track and control modifications.
Complaint Handling & Post-Market Surveillance
Your Commitment to quality doesn’t end when the product leaves your facility. Post-market surveillance is critical to FDA compliance, ensuring that you detect and address safety concerns before they escalate into recalls or regulatory actions.
Your plan should include:
✔ A structured complaints handling process that complies with 21 CFR 820.198.
✔ A system for monitoring adverse events and customer feedback.
✔ Procedures for reporting serious safety issues to the FDA (e.g., MDR for medical devices).
Bonus Tip: A centralized complaints management system ensures nothing falls through the cracks.
But how do you ensure your FDA Quality Plan aligns with evolving regulations and best practices? Review the official US FDA guidelines to ensure your plan meets every requirement.
US FDA Quality Plan Guidelines: What You Need to Know
Creating a US FDA Quality Plan isn’t just about internal policies—it must align with official FDA guidelines to ensure Compliance. The FDA has clear expectations for how organizations should manage quality, risk, and regulatory processes. Failing to meet these guidelines can result in Form 483 observations, warning letters, product recalls, or legal action.
So, how do you ensure your Quality Plan meets FDA expectations? Here’s a deep dive into the key regulations, requirements, and best practices you must follow.
FDA Quality System Regulation (QSR) – 21 CFR Part 820
This is the most critical standard for medical device manufacturers and outlines the minimum quality system requirements for Compliance.
Key Requirements Under 21 CFR Part 820:
✔ Documented Quality System – Your QMS must be defined, implemented, and maintained.
✔ Management Responsibility – Executives must be actively involved in quality planning and reviews.
✔ Design Controls – Clear design verification, validation, and risk management processes.
✔ CAPA (Corrective & Preventive Actions) – A system for proactively identifying and addressing quality issues.
✔ Complaint Handling – A structured approach to collect, analyze, and respond to customer complaints.
✔ Production & Process Controls – Procedures for ensuring consistent, high-quality manufacturing processes.
21 CFR Part 11 – Electronic Records & Signatures
This regulation ensures data integrity and security if you’re using electronic records, documentation, or signatures.
Key Requirements Under 21 CFR Part 11:
✔ Electronic Signatures – Must be unique, verifiable, and linked to specific individuals.
✔ Audit Trails – Every change or update to a record must be tracked and time-stamped.
✔ Data Integrity Controls – Systems must prevent unauthorized data access or modifications.
✔ Secure Access & Authentication – User roles and permissions must be strictly managed.
ISO 13485 – The Global Medical Device QMS Standard
While ISO 13485 isn’t an FDA regulation, it’s the recognized global standard for medical device quality management systems.
Key ISO 13485 Guidelines That Align With FDA Expectations:
✔ Risk-Based Approach – Prioritizing patient safety and risk mitigation.
✔ Supplier Controls – Ensuring vendors and third parties meet compliance standards.
✔ Documented Processes – Maintaining clear work instructions, procedures, and training records.
✔ Traceability & Recordkeeping – Keeping detailed product history and audit trails.
ICH Q10 – Pharmaceutical Quality System Guidelines
The ICH Q10 model aligns with the FDA’s CGMP (Current Good Manufacturing Practices) for pharmaceutical companies and streamlines global Compliance.
Key Areas Covered in ICH Q10:
✔ Process Performance & Quality Monitoring – Ensuring drug safety and efficacy through ongoing process validation.
✔ Continual Improvement – Encouraging data-driven improvements and preventive actions.
✔ Knowledge Management – Leveraging data analytics for better decision-making and compliance tracking.
FDA’s Risk-Based Approach to Compliance
The FDA has shifted towards a risk-based approach—meaning companies must prioritize compliance efforts based on risk severity.
What This Means for Your Quality Plan:
✔ High-risk products (e.g., life-saving medical devices, pharmaceuticals) require stricter controls and documentation.
✔ Risk-based CAPA ensures you address the most critical issues first.
✔ Supplier qualification should focus on risk—higher-risk suppliers need more frequent audits and monitoring.
Steps to Create a US FDA Device Quality Plan
Now that we’ve covered the why and what of an FDA Quality Plan let’s get into the how. Creating a comprehensive, audit-ready FDA Quality Plan isn’t just about writing a document—it’s about building a strategic quality framework that ensures Compliance, reduces risks, and improves operational efficiency.
Follow these step-by-step guidelines to craft a bulletproof FDA Quality Plan:
Step 1: Assess Regulatory Requirements Specific to Your Industry
Before drafting your plan, you must identify and understand the specific FDA regulations for your business. Different industries have different compliance requirements, so mapping them out is the first step.
Step 2: Define Your Quality Objectives & Key Performance Indicators (KPIs)
Your FDA Quality Plan should not just be a compliance document—it should drive continuous improvement. That’s why defining measurable quality objectives and KPIs is crucial.
Step 3: Establish Documentation & Recordkeeping Procedures
FDA compliance = strict documentation controls. Every process, decision, training, and quality-related activity must be recorded appropriately.
Step 4: Implement a Risk-Based CAPA & Change Management System
The FDA wants you to proactively identify and address quality issues before they become significant problems. That’s why risk-based CAPA Management and Change Management are must-haves in your plan.
Step 5: Build a Supplier & Vendor Compliance Program
Your FDA compliance isn’t just about internal processes—it extends to your entire supply chain. That means your suppliers must also follow strict quality controls.
Step 6: Ensure Employee Training & Compliance Awareness
Your Quality Plan is only as strong as the people who execute it. That’s why training is a critical step in FDA compliance.
Step 7: Implement Audit-Ready Monitoring & Continuous Improvement
FDA inspections can happen at any time. You need real-time monitoring tools to track Compliance, spot issues early, and maintain audit readiness.
Crafting an Effective US FDA Quality Plan with Qualityze
Now that we’ve laid the groundwork for creating an FDA-compliant Quality Plan, it’s time to talk about how you can streamline and automate the process using Qualityze.
Gone are the days of juggling spreadsheets, paper-based documents, and disconnected systems that slow down compliance efforts. With Qualityze EQMS, you get an intelligent, cloud-based platform that ensures every aspect of your FDA Quality Plan is compliant but also efficient, scalable, and audit-ready.
Let’s quickly look at how Qualityze helps you devise an FDA Quality Plan for success:
1. Centralized Secure Cloud Platform
Managing quality-related activities manually is inefficient and prone to compliance risks. Qualityze's cloud-based platform centralizes all quality data, ensuring secure document control, automated approvals, and real-time tracking—all compliant with FDA 21 CFR Part 11. Whether you’re a startup or an enterprise, Qualityze scales to your needs, eliminating the chaos of scattered records. When the FDA comes knocking, everything is accessible, organized, and traceable—no scrambling required.
2. Fully Integrated CAPA & Change Management
An effective CAPA and Change Management system is critical to FDA compliance, yet legacy processes often create bottlenecks. Qualityze automates CAPA workflows, ensuring timely identification, investigation, and resolution of quality issues. Integrated change control helps track modifications seamlessly, while AI-powered risk analysis proactively detects compliance risks before they escalate. Faster CAPA resolution means lower compliance risks and better audit outcomes.
3. Automated Supplier Quality Management
Your supplier’s Compliance directly impacts your FDA readiness, making supplier qualification, audits, and monitoring essential. Qualityze automates supplier onboarding, real-time scorecards, and corrective action tracking (SCARs) to ensure vendors meet strict quality standards. By eliminating manual oversight gaps, businesses can reduce the risks of supplier-related recalls, non-conformance, and regulatory penalties.
4. Streamlined Training & Compliance Awareness
Training compliance is more than just checking a box—it’s about ensuring every employee handling quality-sensitive processes is well-prepared. Qualityze automates training schedules, tracks completion status, and manages certifications with e-signatures, ensuring Compliance with regulatory standards. Proactive training prevents human errors, reduces operational risks, and strengthens FDA compliance.
5. Real-Time Audit Management & Continuous Improvement
Audits shouldn’t be a fire drill—they should be an ongoing compliance strategy. Qualityze simplifies audit management with automated internal and external audit scheduling, AI-driven compliance insights, and instant access to audit trails. Whether facing an FDA inspection or an internal compliance review, businesses remain audit-ready with full traceability and risk visibility.
6. Post-Market Surveillance & Complaint Management
FDA compliance doesn’t end after production—tracking and managing customer complaints is crucial to avoid regulatory action. Qualityze automates complaint intake, integrates adverse event reporting (MDR, eMDR, FDA submission), and links issues to CAPA processes, ensuring swift resolution. Proactive complaint handling prevents recalls, protects brand trust, and enhances product safety.
Final Thoughts
Achieving compliance excellence with outdated systems may get overwhelming. Choose next-generation tools like Qualityze. It is a cloud-based, AI-driven QMS that simplifies end-to-end quality, safety, and compliance management. Beyond regulatory mandates, Qualityze helps build a resilient, quality-first culture.
Don’t wait for an FDA audit to reveal compliance gaps. Take control today! Talk to our experts to explore how Qualityze can streamline your quality processes or request a personalized demo to see it in action.
Share
The Start of Something Amazing.
Request Demo
Products
Industries