Table of Content
1 What Is Quality Risk Management?
2 Why is QRM Important?
3 How to Make QRM Work for You: A Step-by-Step Playbook
4 Quality Risk Management: A Tailored Approach for Every Challenge
1. Industry-Specific QRM: Where One Size Doesn’t Fit All
2. Process Scope: Go Big or Go Focused
3. Strategy: Play Offense or Defense?
8 QRM Tools: Your Risk-Busting Arsenal
9 Principles: The Heartbeat of Effective QRM
10 Making QRM Stick
The Good, the Bad, and the Ugly: QRM Challenges
12 Why Bother? The Payoff
13 Qualityze: The Next Generation Risk Management Solution Designed for You!
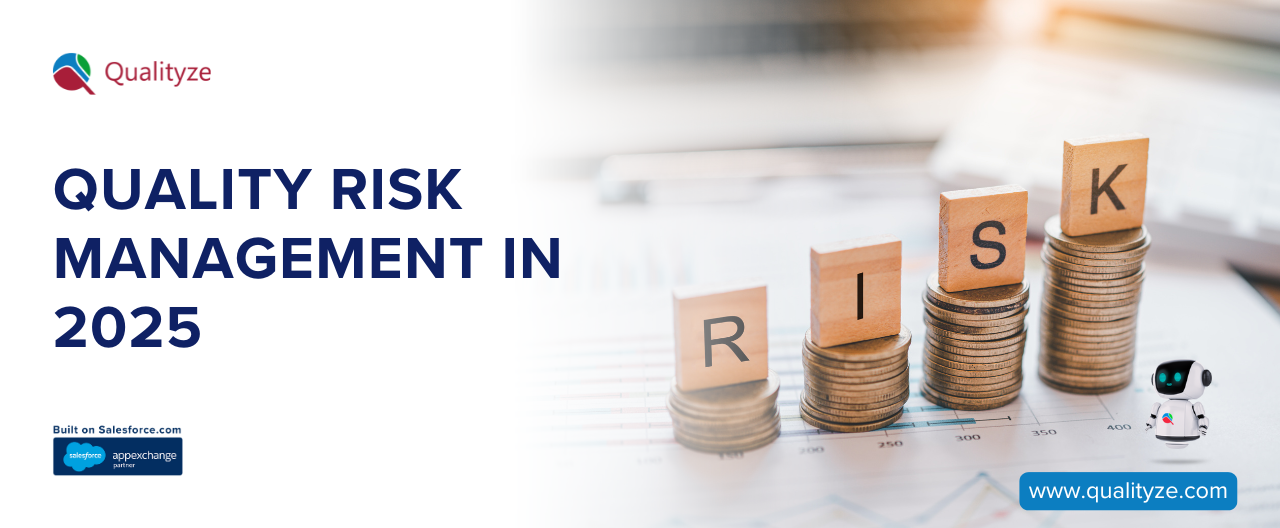
Ever lie awake at night stressing about product recalls, audits, or that nagging feeling you’ve missed a critical step in compliance? If you’re a quality manager, compliance officer, or manufacturing lead, we get it. The daily grind of meeting regulations and chasing down risks can feel like running on a treadmill—always moving, never quite ahead. Enter Quality Risk Management (QRM). But what exactly is it, and why does it deserve a spot on your priority list?
Let’s cut through the jargon. Picture this: You’re baking a cake. Instead of waiting to see if it collapses in the oven, you check the batter consistency, preheat the oven properly, and set a timer. That’s QRM in a nutshell—spotting potential disasters before they happen. It’s not just about ticking boxes for the FDA or ISO audits. It’s about building a safety net so reliable, you can sip your coffee during inspections, knowing your processes are rock-solid.
Let’s get started.
What Is Quality Risk Management?
QRM isn’t some abstract theory. It’s your playbook for asking, “What’s the worst that could happen?”—and then making sure it doesn’t. Officially, it’s a systematic way to identify, assess, and control risks in product quality. Unofficially? It’s the difference between a “smooth sailing” quarter and a “why is the CEO in my office?” kind of day.
Imagine a car’s GPS rerouting you around traffic jams. QRM does the same for your operations, steering you clear of defects, compliance hiccups, and angry customer calls.
Why is QRM Important?
QRM is not just for compliance’s sake. It’s a mindset shift:
-
Stop Problems Before They Start: Catch issues when they’re still glitches, not crises.
-
Audit-Proof Your Processes: Turn “Oh no, the FDA’s here” into “Welcome, let’s grab the good coffee.”
-
Save Time (and Sanity): Fewer fire drills mean more time for strategic wins.
-
Build Trust: Consistent quality = loyal customers + a reputation that opens doors.
How to Make QRM Work for You: A Step-by-Step Playbook
-
Risk Assessment: Brainstorm every possible “what if.” (Yes, even the absurd ones.)
-
Risk Control: Assign action steps—like assigning a babysitter to high-risk processes.
-
Communication: Ditch the silos. Share risks across teams like weekend gossip.
-
Review: Treat your QRM plan like a Netflix subscription—regularly check if it’s still worth keeping.
Quality Risk Management: A Tailored Approach for Every Challenge
Quality Risk Management (QRM) isn’t a rigid checklist—it’s more like a toolkit. Just as you wouldn’t use a hammer to fix a leaky pipe, different industries and organizations need strategies that fit their unique risks. Let’s break down how QRM adapts to diverse needs, and how you can craft a strategy that works like a glove.
1. Industry-Specific QRM: Where One Size Doesn’t Fit All
Every sector has its own "Achilles’ heel." Here’s how QRM tackles them:
-
Pharmaceuticals & Healthcare: Life-Saving Precision
Imagine a drug manufacturer racing to launch a new medication. One overlooked contamination risk could delay approval—or worse, harm patients. That’s why pharma and healthcare lean on rigorous risk assessments and 24/7 monitoring. Tools like FMEA (Failure Modes and Effects Analysis) act like a microscope, scrutinizing every step to ensure compliance with FDA or EMA regulations. It’s not just about avoiding fines; it’s about trust.
-
Manufacturing & Electronics: Keeping the Gears Turning
Picture an automotive assembly line. A single defective part could halt production for days. Manufacturers rely on Statistical Process Control (SPC) to catch variations in real-time—think of it as a dashboard warning light for quality. Techniques like FMEA also help teams anticipate bottlenecks, like a faulty sensor disrupting a robotics line. The goal? Consistency, efficiency, and fewer midnight fire drills.
-
Food & Beverage: Safety First, Always
A recall over contaminated produce can tank a brand overnight. Food companies live by Hazard Analysis and Critical Control Points (HACCP)—a system that’s part detective, part safety net. It identifies critical junctures where hazards (like bacterial growth) could sneak in, then sets up safeguards. Ever wonder how your salad stays pathogen-free? Thank HACCP.
2. Process Scope: Go Big or Go Focused
QRM isn’t all-or-nothing. It’s about finding the right scale:
-
Enterprise-Wide QRM: The Big Picture Play
This is for organizations that want quality woven into their DNA. Think of a tech giant ensuring every team—from R&D to customer support—shares the same risk language. It’s like building a symphony: alignment across departments means fewer surprises and smoother operations.
-
Departmental QRM: Precision Targeting
Not ready for a company-wide overhaul? Start where it hurts. A medical device company might zero in on their sterilization process, using deep-dive risk assessments to avoid recalls. It’s like reinforcing the weakest link in a chain first.
3. Strategy: Play Offense or Defense?
-
Proactive QRM: Stay Ahead of the Curve
Proactive teams don’t wait for disasters. They run regular “what-if” drills, like a football team practicing for every possible play. Continuous monitoring tools, such as SPC charts, act as early-warning systems. For example, a spike in factory humidity levels could trigger alerts before electronics components corrode.
-
Reactive QRM: Damage Control Mode
Even the best plans can’t predict everything. When a supplier suddenly delivers faulty materials, reactive QRM kicks in—think of it as an emergency brake. Root Cause Analysis (RCA) helps teams dissect the “why” behind the issue. But relying solely on this? It’s like mopping the floor while the faucet’s still running. Blend it with proactive steps for balance.
QRM Tools: Your Risk-Busting Arsenal
Risk Assessment Classics
-
FMEA: The Swiss Army knife of QRM. It ranks risks by severity, frequency, and detectability. (Example: A carmaker using FMEA to prevent brake failure risks.)
-
HACCP: The food industry’s guardian angel, pinpointing critical control points like storage temps or packaging integrity.
Data-Driven Insights
-
SPC: Real-time dashboards tracking production metrics. A chocolate factory might use it to ensure every bar weighs exactly 100g.
-
RCA: The “Five Whys” technique—ask why a problem happened until you hit the root. (Why did the machine fail? A worn-out part. Why was it worn? Lack of maintenance checks…)
Principles: The Heartbeat of Effective QRM
-
Be a Fortune Teller
Anticipate risks early. A pharma company might simulate supply chain disruptions to avoid drug shortages.
-
No Secrets, No Silos
Transparency builds trust. If a line worker spots a defect, they should feel safe shouting it out—no red tape.
-
Iterate, Don’t Stagnate
QRM isn’t a “set it and forget it” crockpot. Regular reviews keep it fresh, like updating your phone’s OS.
-
Compliance as a Compass
Align with standards like ISO 9001 not just to pass audits, but to benchmark excellence.
-
Let Data Lead
Replace gut feelings with hard evidence. Example: Using SPC data to justify investing in better factory sensors.
-
Empower Every Employee
When a warehouse team suggests a safer stacking method, listen. Great ideas often come from the front lines.
Making QRM Stick
The magic happens when tools meet culture. Train teams to see QRM not as red tape, but as their daily armor against chaos. Share stories: “Remember when RCA saved us from that packaging disaster?” Celebrate wins, learn from near-misses, and keep the conversation alive.
QRM isn’t just about avoiding pitfalls—it’s about paving a smoother, smarter path forward. Ready to tailor yours?
The Good, the Bad, and the Ugly: QRM Challenges
Let’s be real—QRM isn’t always a walk in the park:
-
“But We’ve Always Done It This Way!”: Combat resistance with quick wins. Show how QRM simplifies someone’s daily grind.
-
Budget Woes: Start small. Focus on one high-impact process, prove ROI, then scale.
-
Data Overload: Ditch manual tracking. Tools like Qualityze turn data chaos into actionable insights.
Why Bother? The Payoff
Companies that nail QRM don’t just survive—they thrive:
-
Fewer Midnight Emergencies: Proactive fixes mean fewer 2 a.m. panic calls.
-
Happy Customers, Happy CFO: Consistent quality = repeat business + fewer refunds.
-
Culture Upgrade: Teams feel empowered, not reactive.
Qualityze: The Next Generation Risk Management Solution Designed for You!
Our AI-Powered, cloud-based solution is designed for real people juggling real deadlines:
-
Automate the Mundane: Let bots handle risk scoring while you focus on strategy.
-
Stay Audit-Ready 24/7: Dashboards show compliance status at a glance—no last-minute scrambles.
-
Grow Without the Growing Pains: Scale from a single facility to global operations seamlessly.
Ready to ditch the outdated systems?
QRM isn’t about avoiding risks—it’s about mastering them. Whether you’re a startup or a Fortune 500, the right approach turns quality from a cost center into your competitive edge.
So, next time you’re tempted to skip a risk review, ask yourself: “Do I feel lucky?” Or, book a demo with Qualityze and let’s make luck irrelevant.
Share
The Start of Something Amazing.
Request Demo
Products
Industries