Table of Content
1 Introduction to QMS Audits in Regulated Industries
Defining QMS Audits
3 Why Audits Matter in Regulated Industries
4 Emerging Challenges and Opportunities
5 Key Regulatory Frameworks and Standards
Overview of Global Regulations
Important ISO Standards
Industry-Specific Compliance Requirements
9 Foundations of a Quality Management System (QMS)
Core Elements of a QMS
Risk-Based Thinking
Continuous Improvement Cycles
13 Preparing for a QMS Audit
Defining Audit Objectives and Scope
Creating the Audit Plan
Training and Empowering the Audit Team
Pre-Audit Checklists and Documentation
18 When Conducting the Audit: Processes and Best Practices to Follow
Opening Meeting and Communication
On-Site Observations and Interviews
Data Collection and Record Review
Audit Findings and Non-Conformities
23 Smarter Tools and Technologies for QMS Audits
Robust Audit Management Solutions
Digital Documentation and Electronic Records
Data Analytics and Real-Time Monitoring
AI in QMS Audits
Cloud-Based Collaboration
29 Post-Audit Activities and CAPA Management
Analyzing Audit Results
Implement Effective Corrective and Preventive Actions (CAPA)
Communicating Outcomes and Lessons Learned
Follow-up audits for Continuous Improvements
34 Building a Culture of Quality and Compliance
Leadership Engagement and Support
Employee Awareness and Training
Measuring Culture and Maturity
Innovative Approaches and Future Trends
39 Key Takeaways
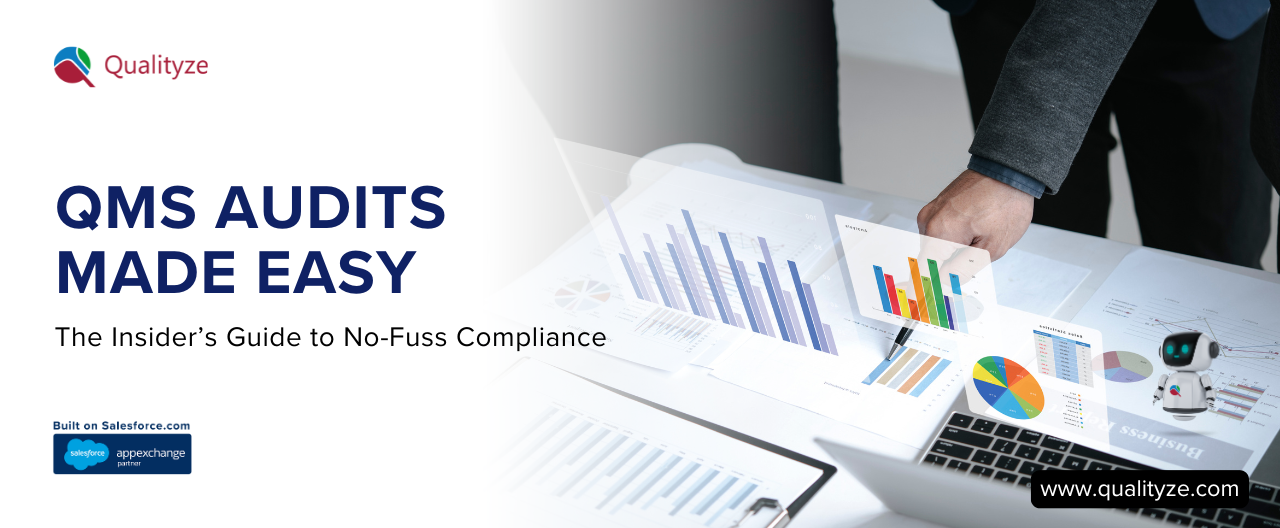
When you work in a regulated industry, follow best practices day in and day out, and have all your compliance documentation in place, nothing really bothers you.
Then comes your audit reminder; just like that, the air thickens with apprehension. You start stressing out more, double-checking everything, and pushing your teams harder. If this sounds relatable, something is surely not right—either in your processes or your approach.
Audits don't have to be the creativity-stifling event we so often dread. They serve as catalysts for fresh thinking, robust processes, and a healthier culture of continual growth. We only need to reimagine them— as invaluable tools for continuous improvement and growth. That mindset shift -from fear to possibility- is precisely what we need to explore to hit the balance right with QMS Audits.
Introduction to QMS Audits in Regulated Industries
Defining QMS Audits
Let's begin by clarifying what we mean by saying "QMS audit." Simply put, a QMS audit is like a thorough checkup for your Quality Management System. Just as a doctor assesses your vital signs, an auditor looks at your processes, documentation, and overall approach to quality to see if everything's functioning as it should.
Ever wonder who does these audits? Sometimes, it’s your own team checking things out (that’s called an internal audit). Other times, outside experts—like regulators, certification bodies, or independent auditors—come in to take a look (that’s an external audit).
And the main reason for all this? To make sure you’re following your own documented processes, standards and regulations specific to your industry.
Why Audits Matter in Regulated Industries
You might wonder: "Do audits matter that much?"
The answer is a resounding "Yes!"
In regulated sectors—like pharmaceuticals, medical devices, or even food production—a compliance slip-up can cause huge monetary losses, reputational damage, or even harm to consumers. Audits serve as that safety net, catching minor issues before they snowball into major problems.
Audits also give you peace of mind. They assure you, your team, and your stakeholders that your business operations stand on solid ground. So, when regulators knock, you'll be prepared instead of scrambling at the last minute.
Emerging Challenges and Opportunities
These days, businesses face more complexity due to multiple regulatory frameworks, diverse customer needs, and rapidly evolving technologies. It can feel daunting, right? But here's the good news: the tools that make our industries more complex also help us manage that complexity more effectively.
Automation, data analytics, and AI-driven insights can transform how you approach audits. Audits are no longer just a paperwork exercise; they become a more proactive and data-driven ongoing process. You'll soon see that harnessing these smarter tools can turn compliance into a competitive advantage rather than a burdensome obligation.
Key Regulatory Frameworks and Standards
Overview of Global Regulations
No two markets function exactly alike. For instance, in the United States, the FDA oversees food, drugs, and medical devices, while in the European Union, the EMA (European Medicines Agency) handles similar products. Outside these major players, every country often has its own set of rules.
Understanding the core principles common among these regulators—like the emphasis on product safety, efficacy, and transparency—is important. Once you grasp these, adapting to specific local requirements becomes much easier.
Important ISO Standards
If you've worked with quality management, you've probably heard of ISO standards. Think of ISO 9001 as your foundational blueprint for a robust Quality Management System. It offers guidelines on everything from leadership and planning to performance evaluation.
ISO 13485 is more specialized for medical devices, focusing on device-specific quality processes. Other industries have their own specialized ISO standards, but most revolve around the same concept: creating reliable, repeatable processes that keep quality front and center.
Industry-Specific Compliance Requirements
-
Pharmaceuticals and biotech: Stringent guidelines like GxP, thorough and controlled documentation, and strict labeling requirements.
-
Medical devices: Emphasis on product design, risk management, and post-market surveillance.
-
Food and beverage: Ensuring safety from farm to fork, with an eye on hygiene standards and traceability.
Regardless of your sector, the common thread is ensuring that what you produce—or the service you deliver—meets strict safety and quality benchmarks. Of course, QMS audits help verify just that.
Foundations of a Quality Management System (QMS)
Core Elements of a QMS
Think of it like the strong foundation of a house—it supports everything related to keeping your work at a high standard. A QMS usually has a few key parts:
-
Document control: This means keeping all important papers (like procedures, forms, and records) up to date and easy for everyone to find.
-
Organizational structure: Here, you figure out who does what job, who reports to whom, and how everyone fits together on the team.
-
Management oversight: This is all about leaders setting a good example. They make sure people have what they need to do their jobs well and set clear goals for quality.
When all these pieces come together, you have a solid system that helps everyone do their best work. It’s like having a sturdy frame that holds everything in place and keeps things running smoothly!
Risk-Based Thinking
Imagine you’re talking with an FDA inspector. In the past, they might have followed a long list of “Do this, check that.” But now they’re more focused on where things could go wrong. In other words, they want you to spot possible problems and fix them before they happen—instead of just waiting for mistakes to pop up and then scrambling to fix them. This means you should carefully examine each process step-by-step, ask, "What could go wrong here?" and then implement controls to prevent or mitigate those issues. Advanced risk assessment tools like Failure Mode and Effects Analysis (FMEA) can help make this more systematic.
Continuous Improvement Cycles
The Plan-Do-Check-Act (PDCA) cycle is at the heart of continuous improvement. When you integrate PDCA into your daily operations, audits become less of a "here we go again" moment and more of an ongoing, beneficial process. You plan improvements, implement them, check the results, and then act to refine them further. That cycle keeps your QMS fresh and responsive to change.
Preparing for a QMS Audit
Defining Audit Objectives and Scope
Before you dive into an audit, be very clear about your intent and why you're doing it.
-
Are you aiming to meet a particular regulatory requirement?
-
Are you preparing for an external inspection?
Pinpoint all your objectives so the audit focuses on the right areas, and you don't waste time chasing irrelevant details.
Creating the Audit Plan
Once you've nailed down the why, the next step is the how. Plan a timeline, decide who will be involved, and specify which documents or processes you'll review. Think of the audit plan as the "itinerary" for your audit journey. A detailed plan keeps your team and stakeholders on the same page and reduces the chances of expensive surprises.
Training and Empowering the Audit Team
Not everyone is cut out to be an auditor. You need people who are detail-oriented, methodical, and knowledgeable about your industry. They also have to be good communicators—nobody wants an auditor who makes people feel interrogated! Provide training on relevant regulations, auditing techniques, and soft skills like interviewing and conflict resolution.
Pre-Audit Checklists and Documentation
Checklists are like your absolute best friend for audits. Think about it: they help you remember all those tiny little details so you don't accidentally skip something important. And if you've taken the time to pull together all your documents in advance, you won't be running around at the last minute, totally losing your mind trying to track down that one piece of paper you forgot. Seriously, you'll thank yourself later for being prepared!
When Conducting the Audit: Processes and Best Practices to Follow
Opening Meeting and Communication
The opening meeting really kicks things off. It's when you introduce the auditors, review what the audit will cover, and sort out the logistics. Plus, it's a great moment to remind everyone that this is a team effort to improve things.
On-Site Observations and Interviews
Imagine the auditors as friendly visitors. They'll stroll through your workspace, watch how you handle daily tasks, and chat with your team to see how everything works. That’s really all there is to it—think of it like a quick checkup for your business.
Data Collection and Record Review
Documentation is everything. SOPs, training records, quality control data—you name it. Your audit team will review these documents to see if the practice matches the policy. Any inconsistency between "what you say you do" and "what you actually do" is a red flag.
Audit Findings and Non-Conformities
After checking everything out, auditors combine their observations into "findings." Now, those findings could be small issues that you can fix pretty easily, or they might be bigger problems—ones that are a little scarier and need your immediate attention. No matter how you look at it, these findings are like handy hints that guide you toward doing things better—almost like having a personal roadmap to help you grow and improve!
Smarter Tools and Technologies for QMS Audits
Robust Audit Management Solutions
Are you tired of shuffling through heavy binders and endless spreadsheets just to manage your audits? That’s no way to work in today’s fast-paced world. Instead, consider using a modern Audit management tool like Qualityze. It brings all your audit activities—planning, scheduling, and reporting—under one roof. Plus, it sends out automatic alerts, offers handy templates you can tailor to your needs, and shows everything on easy-to-read dashboards. It’s like having a personal assistant for your audits, helping you save time and avoid headaches.
Digital Documentation and Electronic Records
Going paperless doesn't just save trees; it also makes your life easier. Electronic records can be quickly searched, shared, and updated. In regulated industries, you'll need to ensure compliance with rules like 21 CFR Part 11 or Annex 11 for EU (for electronic signatures and records), but the efficiencies you gain are well worth the effort.
Data Analytics and Real-Time Monitoring
Picture this: a sensor on your production line spots a temperature spike that could compromise product quality. Would you rather learn about it days later—or stop it in its tracks immediately? That's where real-time monitoring comes in. You can keep an eye on quality parameters by using sensors, IoT devices, and dynamic data visualization tools. And if something seems off, you can trigger alerts or corrective actions immediately, preventing a small issue from exploding into a big headache.
AI in QMS Audits
You've probably heard the buzz about AI. It has transformed quality processes with advanced algorithms that detect unusual trends in massive datasets and even predict which processes are at higher risk of failing. Of course, the technology and the regulatory guidelines around it are still evolving, so proceed with a bit of caution. But if you're eager to be on the cutting edge, AI-driven audits could be a real game-changer for your organization.
Cloud-Based Collaboration
Nowadays, teams are spread across different countries—sometimes even different continents. That's why cloud-based platforms are so handy. They let everyone see the same audit documents, reports, and checklists simultaneously. When people share information this easily, decisions are made faster, and everybody stays on the same page.
Post-Audit Activities and CAPA Management
Analyzing Audit Results
After you wrap up an audit, you'll want to make sense of all the findings. One practical approach is to group observations by risk level, department, or process. This helps you spot patterns—maybe there's a recurring training gap in one area or a consistent issue at a certain step in your workflow. By organizing your data, You can make better improvement efforts.
Implement Effective Corrective and Preventive Actions (CAPA)
When your audit points out a gap, slapping on a quick fix might hold things together for now, but it won’t take care of the real issue. You’ve got to dig a little deeper and find out why it happened in the first place. That’s the only way to make sure it doesn’t come back to haunt you.
Now, let's talk about how you fix it.
-
Corrective actions are great for handling immediate trouble. They're like a bandage for the wound.
-
Preventive actions prevent the wound from coming back. They tackle the underlying reasons so the problem doesn't happen again.
A solid CAPA (Corrective and Preventive Action) process is like the backbone of long-term quality improvement. It helps you stay on track and keep growing without tripping over the same issues again and again.
Communicating Outcomes and Lessons Learned
Open communication builds trust, both within your team and with external stakeholders. So, once you've got the audit results, share them. Talk about what went well—celebrating wins boosts morale—and be transparent about where to improve. It's all about collective learning, not pointing fingers.
Follow-up audits for Continuous Improvements
Even after regulatory bodies have placed so much emphasis on audits, some companies still consider them a one-time event. They must realize the need for continuous improvements and follow-up audits to confirm that their resolutions or action plans actually worked to mitigate gaps and inefficiencies.
Plus, scheduling these check-ins shows you're serious about quality—it's an ongoing commitment to improving.
Related Article: Role of Audit Management Software: From Compliance to Performance
Building a Culture of Quality and Compliance
Leadership Engagement and Support
It will be an uphill battle if your senior leaders aren't fully behind your quality initiatives. Leaders set the tone by allocating resources, providing clear direction, and recognizing people committed to quality. When top-level executives support compliance and a culture of quality, the rest of the organization automatically follows best practices.
Employee Awareness and Training
Quality is everyone's job, from the shop floor to the boardroom. Regular training sessions, straightforward SOPs, and a culture where questions are encouraged go a long way toward making quality a shared responsibility. You want each employee to think, "How can I help maintain and improve our standards?"—not, "That's the QA team's problem."
Measuring Culture and Maturity
Saying you have a "culture of quality" is one thing; proving it is another. Use tools like employee surveys, internal audits, and performance metrics to see how deeply quality practices are embedded. Over time, you'll get a clear picture of your organizational maturity—and you'll be able to pinpoint exactly where you need to step up your game.
Innovative Approaches and Future Trends
Remote audits are becoming more common, especially after global disruptions like the pandemic. These partially or fully virtual audits can save time and resources but require careful planning and robust digital tools. As new technologies evolve, we'll see audits shift from a periodic "event" to a constant, data-driven process that spots and resolves issues before they escalate.
Key Takeaways
The blog provides detailed information on how QMS audits in regulated industries have become indispensable and increasingly tech-driven. Your should priortize delivering safe, high-quality products and services while staying compliant. The tools like cloud-based audit management solutions, real-time monitoring, and AI can make your processes smarter and more efficient.
Here's an effective action plan for continuous improvement:
-
Embrace Digital Tools: Move to electronic records, adopt audit management software, and explore data analytics.
-
Train Continuously: Keep your team updated on relevant regulations and the latest auditing techniques.
-
Engage Leadership: Keep your top management informed and involved to ensure the necessary resources and consistent cultural support.
-
Follow-Up Diligently: Don't let corrective actions fall through the cracks—schedule follow-up audits to confirm effectiveness.
-
Stay Future-Focused: For proactive quality management, monitor emerging technologies like AI, machine learning, and IoT.
If you follow the steps mentioned earlier to excel in a culture of ongoing improvement, you'll be well on your way to building a compliant QMS that is a true driver of excellence.
Share
The Start of Something Amazing.
Request Demo
Products
Industries