Overcoming the Negative Reputation of CAPA in Organizations: A Guide to Effective Implementation
Table of Content
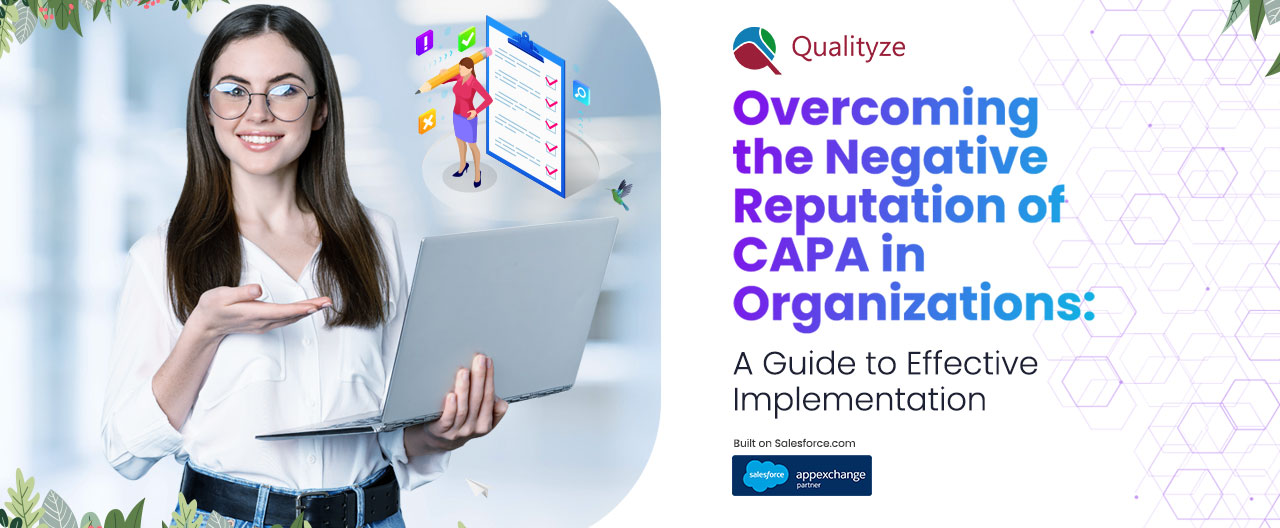
Qualityze Podcast : Overcoming the Negative Reputation of CAPA in Organizations: A Guide to Effective Implementation
Today, we will discuss something that has a negative reputation in many organizations – CAPA.
Corrective and Preventive Action (CAPA) is a vital part of any quality management system, but it often gets a bad rap. Some employees see it as a burden, a waste of time, or even a punishment for mistakes. However, this negative perception can be overcome with the right approach.
For example, let’s say you work in a manufacturing company that produces electronic devices. You have noticed that there have been several incidents of defective products in the past few months, and it’s becoming a serious problem. Your boss has suggested implementing a CAPA Management Solution to address the issue, but many of your colleagues are resistant. They worry that it will create more paperwork and bureaucracy and be time-consuming and frustrating.
In this blog, we’ll explore some common misconceptions about CAPA and provide a guide to effective implementation. We’ll cover everything from setting clear objectives and defining roles and responsibilities to communicating the benefits of CAPA to employees and ensuring that it becomes an integral part of your company’s culture. By the end of this blog, you’ll better understand how to overcome the negative reputation of CAPA and make it a valuable tool for improving the quality of your products and services. So, let’s get started!
A Quick Introduction to CAPA
A CAPA (Corrective and Preventive Action) is approach organizations use to identify, evaluate, and address problems and issues in their operations.
However, there are many misconceptions about CAPA. Some people see it as just another bureaucratic process that slows production, while others view it as a necessary evil to appease regulators. But the truth is CAPA can be a powerful tool for improving quality, reducing costs, and enhancing customer satisfaction.
Related Article: Top 5 CAPA Management Software Systems in 2023
Let’s dig deeper into misconceptions about CAPA.
Misconception #1: CAPA is just another bureaucratic process
One of the most common misconceptions about CAPA is that it’s just another bureaucratic process that slows production and adds unnecessary paperwork. While it’s true that CAPA can involve some paperwork and documentation, its primary goal is to identify and correct problems that can impact the quality of your products or services.
To implement CAPA effectively, it’s important to set clear objectives and communicate them to your team. Make sure everyone understands why CAPA is important and how it can benefit your company in the long run. By involving your team in the process and empowering them to take ownership of CAPA, you can help to shift the perception of CAPA from a bureaucratic process to a powerful tool for continuous improvement.
Misconception #2: CAPA is only necessary to appease regulators
Another common misconception about CAPA is that it’s only necessary to appease regulators and meet compliance requirements. While it’s true that regulatory agencies often require CAPA, its true value lies in its ability to improve the quality of your products or services and enhance customer satisfaction.
To implement CAPA effectively, it’s important to define roles and responsibilities and communicate them clearly to your team. Ensure everyone knows their role in the CAPA process and how it fits into the overall quality management system for manufacturing. By involving your team in the process and highlighting the benefits of CAPA, you can help to ensure that it becomes an integral part of your company’s culture.
Misconception #3: CAPA is only necessary when something goes wrong
Another common misconception about CAPA is that it’s only necessary when something goes wrong. While it’s true that quality issues or customer complaints often trigger CAPA, its true value lies in its ability to prevent problems before they occur.
To implement CAPA effectively, it’s important to communicate the benefits of a proactive approach to quality management. Encourage your team to identify potential issues and take action to prevent them from becoming bigger problems. By integrating a continuous improvement culture into your company and empowering your team to take action, you can help to ensure that CAPA becomes a proactive tool for enhancing the quality and customer satisfaction.
For several reasons, CAPA sometimes lacks a good reputation within organizations despite its importance for continuous improvement. Moreover, it is often seen as an administrative burden or punishment. When employees feel the focus is on punishments and blame rather than improving continuously, they are less likely to buy in and engage.
What are the reasons behind the bad reputation of CAPA?
The bad reputation of CAPA can be attributed to several factors. Some of them are:
It is time-consuming
- Collecting data, performing root cause analysis, and implementing corrective and preventive measures are time-consuming steps in the CAPA process. As a result, CAPA may appear to be a burden rather than a tool for improving performance.
There is a lack of ownership
- Some organizations view CAPA as an individual or departmental task instead of integrating CAPA into their overall continuous improvement culture. The result can be a lack of ownership, accountability, and reluctance to participate.
CAPA process bureaucracy
- Documentation and approval requirements can sometimes make the CAPA process appear bureaucratic and overly formal. This can give the impression that CAPA is mainly about complying rather than improving.
Insignificant impact
- The effectiveness of CAPA depends on its ability to produce meaningful and sustainable improvements. Processes that are poorly designed may not result in meaningful change and may just be box-ticking exercises. As a result, many people believe that CAPA is unnecessary and lack trust in it.
The resistance to change
- Some employees and stakeholders may oppose CAPA implementation because it requires significant changes to processes and systems. For example, CAPA may seem disruptive and unnecessary to the people who are following traditional practices for automotive quality management.
An independent process
- When CAPA is not integrated into the overall quality management system, it can lead to a fragmented approach to continuous improvement. It can result in inconsistent application of CAPA, a lack of standardization, and poor outcomes.
An organization can, however, drive continuous improvement very effectively and efficiently with a robust CAPA process that integrates into the overall quality management system and is supported by senior management and all employees.
In general, overcoming the negative reputation of CAPA requires an efficient, effective, and integrated manner into the organization’s culture of continuous improvement. The key to achieving these results is leading with clarity, committing to continuous improvement, and focusing on the results that CAPA can achieve. Furthermore, it is important to establish clear lines of communication and feedback among all relevant stakeholders. As a result, engagement and participation will increase, as will a sense of ownership and accountability. Finally, a CAPA process should be continuously evaluated and improved to ensure meaningful and sustainable results.
Furthermore, regular training and education on CAPA’s benefits and purpose should be provided to employees and stakeholders. Doing so can make the process more understandable and buy-in can be encouraged for this you can use Qualityze Training Management Software.
As a result, organizations can automate and streamline the CAPA process to minimize bureaucracy and burden. CAPA processes can also be more effective and efficient if employees and stakeholders are involved in the design and implementation. As a final step, tracking and measuring the results of CAPA can lead to an increased understanding of its value and impact and support for its continual improvement.
Our goal at Qualityze is to reduce the time and effort required to manage CAPA processes, improve transparency and visibility, ensure compliance, and enhance collaboration.
Related Article: If You Want to Design a CAPA Resolution Workflow, Follow These Simple Steps
If you want to know how Qualityze CAPA Management helps?
You can reach out to our customer success team through email at info@qualityze.com or by phone at 1-877-207-8616, and they will assist you in effectively implementing the CAPA Management system in your company
Whether you’re just starting or looking to improve your current process, remember that it’s never too late to start. By taking a proactive approach to quality management and embracing the power of CAPA, you can help to drive continuous improvement and achieve long-term success. You can also request a demo for Qualityze CAPA Management and see how it can benefit your company today!
Share
The Start of Something Amazing.
Request Demo
Products
Industries