Table of Content
1 What is a Medical Device Complaint?
Types of Medical Device Complaints
Why Is Complaint Handling So Critical?
4 How to Report Medical Device Complaints
Who Can Report a Medical Device Complaint?
Steps for Reporting a Medical Device Complaint
Common Mistakes in Medical Device Complaint Reporting
8 Medical Device Complaint Handling Process
Step 1: Complaint Reporting to Capture Necessary Details
Step 2: Complaint Triage – Categorization and Risk Assessment
Step 3: Investigation – Finding the Root Cause
Step 4: Implement Corrective and Preventive Actions (CAPA)
Step 5: Regulatory Reporting – Ensuring Compliance
Step 6: Closure and Continuous Monitoring
15 How to Calculate Complaint Rate in Medical Devices
Complaint Rate= (Total Number of Complaints /Total Units Sold or Distributed)×100
How to Reduce Complaint Rate Without Ignoring Valid Complaints
Categorization Based on Complaint Type
19 8 Common Problems in Medical Device Complaint Handling (According to FDA Group)
20 Streamline Complaint Handling with Qualityze QMS for Medical Devices
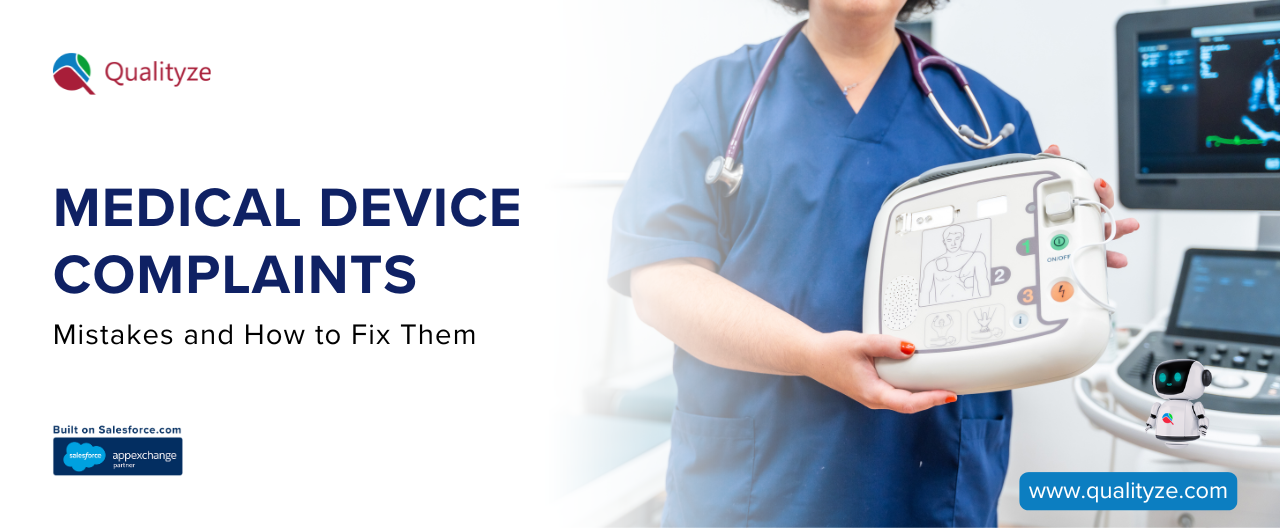
Medical device complaints can be a goldmine of insights—or a regulatory nightmare.
Let’s be honest—regulators take medical device complaints very seriously. The FDA’s 21 CFR 820.198 and ISO 13485:2016 set strict expectations for complaint handling. One misstep, and you could be looking at warning letters, fines, or product seizures.
Every complaint that comes in, regardless of its source, is a signal that something is wrong with processes. You must identify underlying issues before they escalate into recalls, compliance violations, or, worst of all, patients' life risk. Unfortunately, many companies struggle with handling complaints effectively.
So, where do companies go wrong?
According to FDA Group, here are 8 common problems in Medical Device complaint handling;
-
Under-trained or under-experienced intake personnel mis-categorizing genuine complaints from field incidents
-
Inadequate or incomplete service records
-
Improper handling of medical devices with problems (e.g., disposal of malfunctioning units instead of returning them for investigation)
-
Avoidable translation from one language to another, causing inefficiencies and missed details
-
Poor complaint handling procedures leading to user error, incomplete data, and friction
-
Inadequate training for risk assignment and ranking, leading to inaccurate risk assessments
-
Improper medical device complaint classification, resulting in misfiled or unresolved complaints
-
Inefficient or improper closure due to long wait times for cross-functional input, causing complaint backlogs
The good news? You can now manage these challenges easily.
A well-structured Complaint Management System can streamline investigations, improve compliance, and ultimately enhance product quality. By the time you finish reading this blog, you’ll know exactly where most companies fail and—more importantly—how to avoid those pitfalls.
Let’s get started.
What is a Medical Device Complaint?
If you’re in the medical device industry, complaints are inevitable. No product is perfect, and even the most rigorously tested devices can face performance issues, labeling errors, or malfunctions.
According to the FDA (21 CFR 820.198), a medical device complaint is:
"Any written, electronic, or oral communication that alleges deficiencies related to the identity, quality, durability, reliability, safety, effectiveness, or performance of a device after it has been released for distribution.
In simpler terms, if a customer, patient, or healthcare provider reports an issue with your device—even if it’s a minor one—it must be documented and assessed.
Types of Medical Device Complaints
Medical device complaints can range from minor inconveniences to serious safety risks. Here are the most common types:
-
Device Malfunction: The device doesn’t work as intended (e.g., an infusion pump that stops mid-use).
-
Performance Issues: The device works but not as efficiently as expected (e.g., an insulin pump delivering inconsistent doses).
-
Labeling or Packaging Errors: Incorrect instructions, missing safety warnings, or damaged packaging.
-
Biocompatibility Issues: The device causes unexpected reactions when used (e.g., a pacemaker causing skin irritation).
-
Adverse Events & Injuries: The device directly leads to harm or complications (e.g., surgical staplers misfiring and causing internal bleeding).
-
Usability Issues: The device is difficult to use, leading to improper operation and risks (e.g., a ventilator with a confusing interface).
Why Is Complaint Handling So Critical?
One improperly handled complaint can spiral into a major compliance headache. Consider these risks:
-
Regulatory Action like FDA warning letters, fines, or even recalls.
-
Patient Safety Risks leading to adverse events, injuries, or fatalities.
-
Brand Reputation Damage
The Right Approach?
A Structured Complaint Management Proces
Medical device complaints aren’t just problems to fix—they’re opportunities to improve product quality and patient safety. A robust Complaint Management System ensures complaints are properly captured, categorized, investigated, and resolved before they escalate.
🔹 But what’s the right way to report complaints?
🔹 How do you ensure compliance with FDA, ISO 13485, and MDR?
How to Report Medical Device Complaints
Medical device complaints are only valuable if they are properly reported, documented, and investigated. The challenge? Many companies either fail to capture all complaints, misreport them, or overlook regulatory requirements—all of which can lead to compliance risks and product quality issues.
Let’s break down the right way to report medical device complaints, ensuring compliance with FDA, ISO 13485, and MDR regulations.
Who Can Report a Medical Device Complaint?
Anyone who encounters an issue with a medical device can report a complaint, including:
-
Healthcare providers (doctors, nurses, technicians)
-
Hospitals and clinics (medical equipment users, administrators)
-
Patients and caregivers (end-users experiencing issues)
-
Distributors and suppliers (supply chain-related complaints)
-
Internal employees (R&D, quality control, field service teams)
-
Regulatory bodies (FDA, EU MDR authorities)
Even an informal mention of a device issue in an email or phone call or even in casual settings, should be treated as a complaint if it alleges a product defect, malfunction, or safety concern.
Steps for Reporting a Medical Device Complaint
To ensure complaints are properly handled, your organization must follow a standardized reporting process. Here’s how it should work:
-
Step 1: Capture the Complaint
-
Step 2: Categorize and Prioritize
-
Step 3: Investigate the Complaint
-
Step 4: Determine Regulatory Reporting Requirements
-
Step 5: Document and Close the Complaint
Common Mistakes in Medical Device Complaint Reporting
Mistake #1: Ignoring Informal Complaints
Even a casual customer comment about a malfunction should be logged and assessed.
Mistake #2: Failing to Report on Time
Many complaints require mandatory reporting within strict timelines—delays can result in regulatory action.
Mistake #3: Incomplete or Inaccurate Documentation
Missing data in complaint reports can lead to compliance risks and unresolved product issues.
Mistake #4: No Integration with Other Quality Systems
Complaint management should connect with CAPA, Risk, and Change Management systems to prevent recurring issues.
Medical Device Complaint Handling Process
Effectively handling medical device complaints is not just about ticking compliance checkboxes—it’s about ensuring product quality, patient safety, and regulatory adherence. A structured complaint handling process helps organizations reduce risks, prevent future issues, and improve customer trust.
A poorly managed complaint process can lead to regulatory penalties, product recalls, and even liability lawsuits. So, let’s break it down into a step-by-step approach to handling medical device complaints the right way.
Step 1: Complaint Reporting to Capture Necessary Details
The complaint-handling process begins the moment an issue is reported. A structured intake system ensures that all critical details are captured upfront.
✅ Key Information to Capture in the Complaint Intake Form:
-
Reporter Details: Who is submitting the complaint? (Patient, healthcare provider, distributor, internal employee)
-
Device Details: Model number, lot number, serial number, manufacturing date, expiration date.
-
Complaint Description: What exactly happened? (Device failure, performance issue, adverse event, labeling error)
-
Usage Conditions: Where and how was the device used when the issue occurred?
-
Supporting Evidence: Photos, videos, customer statements, incident reports.
Step 2: Complaint Triage – Categorization and Risk Assessment
Not all complaints carry the same level of risk. Some are minor inconveniences, while others may indicate a potential safety hazard. The triage process helps prioritize complaints based on severity and regulatory impact.
Complaint Severity Levels:
Severity Level |
Example |
Action Required |
🔴 Critical |
Device failure leading to patient harm (e.g., pacemaker malfunction) |
Immediate investigation & regulatory reporting |
🟠 Major |
Device defect affecting performance (e.g., infusion pump delivering incorrect dosage) |
Root cause analysis & CAPA required |
🟡 Moderate |
Labeling issues, usability complaints (e.g., confusing instructions) |
Internal assessment & documentation |
🟢 Minor |
Cosmetic or non-functional defects (e.g., minor scratches on non-critical device parts) |
Record and monitor trends |
Step 3: Investigation – Finding the Root Cause
Once a complaint is categorized, it must be investigated to determine:
-
Is it a product defect, user error, or external factor?
-
Is this an isolated issue or part of a broader trend?
-
Does the complaint require regulatory reporting?
Investigation Steps:
-
Review the complaint details to identify patterns or similar past cases.
-
Examine device history (manufacturing records, lot/batch data, inspection reports).
-
Conduct failure mode analysis (FMEA) to determine possible causes.
-
Perform a risk assessment (ISO 14971) to evaluate the impact on patient safety.
-
Document findings and recommended actions in a centralized complaint database.
Step 4: Implement Corrective and Preventive Actions (CAPA)
If the complaint reveals a systemic issue, Corrective and Preventive Action (CAPA) must be initiated.
✔ Corrective Action – Fixing the immediate problem (e.g., recalling faulty batches).
✔ Preventive Action – Implementing process improvements to prevent recurrence (e.g., updating design specifications, enhancing training programs).
Example:
- Complaint: A catheter tubing disconnects too easily.
-
Corrective Action: Issue a field safety notice and update product usage instructions.
-
Preventive Action: Modify the design and manufacturing process to strengthen tubing connections.
Step 5: Regulatory Reporting – Ensuring Compliance
Depending on the severity of the complaint, manufacturers may be required to report the incident to regulatory authorities.
Regulatory Authority-Specific Medical Device Complaint Reporting Timelines
Regulatory Authority |
Reportable Complaints |
Submission Timeline |
FDA (USA) – eMDR |
Serious injury or death cases |
5-30 days |
EU MDR (EUDAMED) |
Incidents affecting device safety or performance |
Immediately (15 days for serious incidents) |
Health Canada |
Issues causing harm or regulatory concern |
10-30 days |
TGA (Australia) |
Faulty or hazardous medical devices |
Varies by severity |
Step 6: Closure and Continuous Monitoring
Once a complaint is resolved:
- Document the entire complaint lifecycle (from intake to resolution).
-
Track similar complaints to detect early warning signs.
-
Use complaint data for continuous product and process improvement.
How to Calculate Complaint Rate in Medical Devices
Tracking medical device complaints is one thing—understanding how they impact your overall quality performance is another. That’s where complaint rate calculation comes in.
A high complaint rate signals potential design, manufacturing, or usability issues, while a low complaint rate (if artificially suppressed due to poor reporting) can lead to compliance risks.
So, how do you calculate and interpret complaint rates effectively? Let’s break it down.
The standard formula for complaint rate is:
Complaint Rate= (Total Number of Complaints /Total Units Sold or Distributed)×100
For example:
-
If you received 250 complaints for a device, and 50,000 units were sold in a given period:
(250/50000) ×100=0.5% Complaint Rate
Industry Benchmark: What is an Acceptable Complaint Rate?
As already mentioned above, there’s no universal standard for acceptable complaint rates, as they vary based on:
-
Device type (e.g., implantable devices have stricter expectations than non-invasive products).
-
Intended use and criticality (e.g., life-supporting devices vs. diagnostic tools).
-
Historical complaint trends for similar products.
Industry-Specific Averages:
Medical Device Type |
Average Complaint Rate |
Implantable Devices (e.g., pacemakers) |
< 0.1% |
Diagnostic Equipment (e.g., MRI scanners) |
|
Disposable Devices (e.g., syringes, catheters) |
0.5% – 1.5% |
Consumer Medical Devices (e.g., hearing aids) |
1% – 3% |
How to Reduce Complaint Rate Without Ignoring Valid Complaints
Lowering the complaint rate isn’t about hiding or ignoring complaints—it’s about improving product quality and preventing recurring issues.
Here are some proven tips to reduce complaint rates:
-
Enhance Supplier Quality Management
-
Strengthen Design Validation & Risk Management
-
Improve Manufacturing & Production Controls
-
Conduct Proactive Customer Training
-
Leverage a Digital Complaint Management System
How Medical Device Complaints Are Categorized
Not all medical device complaints are the same. Some are minor product defects, while others pose serious safety risks requiring immediate regulatory action. Properly categorizing complaints ensures that the most critical issues get prioritized, investigated, and resolved efficiently.
Regulatory bodies like the FDA, EU MDR, and Health Canada require structured complaint categorization to ensure appropriate corrective actions. A poorly categorized complaint can lead to:
-
Delayed investigations - Potentially allowing defective devices to remain in use.
-
Compliance violations – Missing a mandatory regulatory reporting deadline.
-
Wasted resources – Over-investigating minor complaints while serious ones are overlooked.
So, how should medical device complaints be categorized? Let’s break it down.
Classification Based on Severity
-
Critical Complaints (High Risk)
Complaints that indicate a serious device failure, leading to patient injury, death, or regulatory non-compliance.
-
Examples:
-
-
Pacemaker malfunction causing cardiac failure.
-
-
-
Infusion pump delivering an incorrect drug dose.
-
-
-
Defective sterilization in surgical instruments leading to infections.
-
-
-
Major Complaints (Moderate Risk)
-
Complaints that affect device performance but do not pose immediate life-threatening risks.
-
Examples:
-
-
Blood glucose meter shows inaccurate readings.
-
-
-
Catheter tube disconnecting too easily.
-
-
-
MRI scanner misinterpreting imaging data.
-
-
-
Minor Complaints (Low Risk)
-
Complaints related to usability, minor defects, or cosmetic issues that do not affect device functionality or safety.
-
Examples:
-
-
Misspelled words on device labeling.
-
-
-
Packaging dented or torn upon delivery.
-
-
-
Slight discoloration of plastic components.
-
Categorization Based on Complaint Type
Beyond severity, medical device complaints should also be categorized by type, helping manufacturers identify root causes faster.
-
Performance-Related Complaints
Devices that do not function as intended, causing potential risks to users.
-
Examples:
-
-
Surgical staplers failing to close wounds properly.
-
-
-
Defibrillator not delivering the correct shock voltage.
-
-
Safety-Related Complaints
Devices that directly or indirectly harm patients.
-
Examples:
-
-
Implantable devices causing severe allergic reactions.
-
-
-
Drug-eluting stents release incorrect dosage levels.
-
-
Labeling & Packaging Complaints
Issues with instructions, warnings, or packaging materials.
-
Examples:
-
-
Expired sterilization labels on surgical gloves.
-
-
-
Misprinted dosage instructions on medication packaging.
-
-
Usability Complaints
Devices that confuse users due to complex interfaces or poor instructions.
-
Examples:
-
-
An insulin pump with hard-to-navigate settings.
-
-
-
A ventilator with non-intuitive control buttons.
-
8 Common Problems in Medical Device Complaint Handling (According to FDA Group)
-
Under-trained or under-experienced intake personnel mis categorizing genuine complaints from field incidents.
-
Inadequate or incomplete service records
-
Improper handling of medical devices with problems (e.g., disposal of malfunctioning units instead of returning them for investigation)
-
Avoidable translation from one language to another, causing inefficiencies and missed details
-
Poor complaint-handling procedures leading to user error, incomplete data, and friction
-
Inadequate training for risk assignment and ranking, leading to inaccurate risk assessments
-
Improper medical device complaint classification, resulting in misfiled or unresolved complaints
-
Inefficient or improper closure due to long wait times for cross-functional input, causing complaint backlogs
Streamline Complaint Handling with Qualityze QMS for Medical Devices
Here’s how Qualityze transforms complaint handling in medical devices
-
Automates Complaint Intake & Classification with
-
-
A centralized, digital intake system captures complaints from multiple sources automatically.
-
-
-
AI-driven categorization & triage ensures urgent complaints are prioritized instantly.
-
-
Seamless Integration with CAPA & Risk Management for:
-
-
Automated root cause analysis (RCA).
-
-
-
Corrective and Preventive Actions (CAPA) linked to complaints.
-
-
-
Risk-based complaint prioritization using ISO 14971 principles.
-
-
Automates Regulatory Reporting (FDA, EU MDR, Health Canada, etc.) with
-
-
Built-in regulatory reporting workflows ensure timely submission.
-
-
-
Pre-configured templates for FDA MedWatch, EU MDR, and Health Canada reports.
-
-
-
Automated audit trails for seamless compliance audits.
-
-
AI-Powered Complaint Trend Analysis & Recommendations
-
-
AI-driven analytics detect patterns in complaints before they become widespread issues.
-
-
-
Dashboards & Reports provide real-time visibility into product quality trends.
-
-
-
Proactive risk analysis helps manufacturers prevent future complaints proactively.
-
To discover the complete functionalities of Qualityze Complaints Management, request a personalized demo today. Alternatively, you can have a quick consultation call with our customer success executive to assist you.
Share
The Start of Something Amazing.
Request Demo
Products
Industries