Table of Content
1 What is Pharmaceutical Quality Assurance?
2 What is the Role of QA in Pharmaceuticals?
3 Why Is Pharmaceutical Quality Assurance Important?
4 Types of Quality Assurance in the Pharmaceutical Industry
5 Steps to Implement Quality Assurance in the Pharmaceutical Industry
6 Difference Between Pharmaceutical Quality Assurance and Quality Control
7 Role of QMS Software in Supporting Pharmaceutical QA System
8 Conclusion
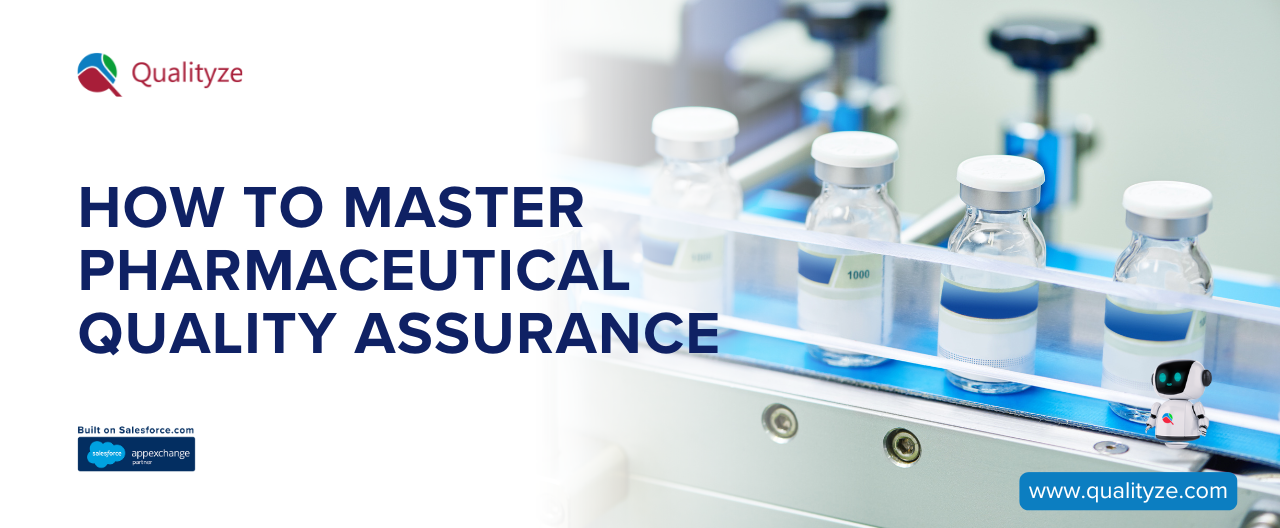
Pharmaceutical Quality Assurance (QA) plays a critical role in the health and safety of consumers. Maintaining product quality has become increasingly challenging as the pharmaceutical industry continues to grow. Poor pharmaceutical QA can have severe consequences, including drug recalls, regulatory penalties, legal liabilities, and even patient harm. According to a study conducted by the World Health Organization, counterfeit and substandard medicines cause more than 100,000 deaths annually worldwide. The cost of failing to implement a robust pharmaceutical QA system is financial and reputational.
For pharmaceutical companies, mastering QA is no longer optional—it is a necessity. One of the best ways to ensure the highest standards of quality assurance is by leveraging technology. The Qualityze EQMS suite effectively addresses these challenges. It streamlines QA processes, ensuring compliance with global regulations like FDA 21 CFR Part 11 and EU Annex 11. Its unique features include automated workflows, real-time monitoring, and advanced analytics. These tools help pharmaceutical companies reduce errors, improve efficiency, and maintain compliance.
What is Pharmaceutical Quality Assurance?
Pharmaceutical Quality Assurance (QA) refers to the systematic activities and practices aimed at ensuring that pharmaceutical products meet the required quality standards. It involves the entire lifecycle of a drug, from development to production and distribution, ensuring safety, efficacy, and compliance with regulatory requirements. Pharmaceutical QA encompasses all procedures, including designing, documenting, implementing, and auditing quality systems to ensure every product is safe for public consumption.
QA is a proactive process aimed at preventing issues before they arise rather than merely detecting and correcting problems after they occur. This approach is essential in the pharmaceutical industry, where product failures can have dire consequences for public health.
What is the Role of QA in Pharmaceuticals?
QA has many roles in pharmaceuticals. It focuses on creating and maintaining systems that guarantee product quality at every production stage. Specifically, QA:
-
Ensures Compliance: Pharmaceutical QA teams ensure that all processes comply with local and international regulations, such as those of the U.S. Food and Drug Administration (FDA) and the European Medicines Agency (EMA). This includes compliance with Good Manufacturing Practices (GMP) and Good Laboratory Practices (GLP).
-
Monitors Production Processes: QA teams monitor every step in the production process, ensuring that the manufacturing environment, raw materials, and finished products adhere to the necessary quality standards.
-
Handles Documentation: QA is responsible for documenting procedures, protocols, testing, and validation processes to provide a clear trail of evidence that all quality standards have been met.
-
Risk Management: QA teams assess potential risks and implement mitigation measures. This includes identifying quality issues and determining solutions to prevent non-conformities.
-
Ensures Consumer Safety: Ultimately, QA's primary responsibility is to ensure that the products being produced are safe, effective, and meet the required quality standards before they reach consumers.
Why Is Pharmaceutical Quality Assurance Important?
The importance of pharmaceutical quality assurance cannot be overstated. According to the U.S. FDA, 30% of drugs approved each year experience some form of manufacturing issue. The consequences of quality failure can be catastrophic for both consumers and the company involved.
-
Health and Safety Risks: Poor-quality drugs can lead to severe health complications. For instance, faulty drugs might fail to deliver the intended therapeutic effect or cause harmful side effects.
-
Regulatory Consequences: Failing to meet regulatory standards can result in drug recalls, legal penalties, and loss of market access. A notable example is the 2012 recall of contaminated drugs by the New England Compounding Center, which led to 64 deaths and hundreds of infections.
-
Financial Loss: A product recall can cost millions of dollars. In fact, according to a study by the Product Recall Institute, the average cost of a drug recall is around $10 million, not including the long-term damage to the company's reputation.
-
Loss of Consumer Trust: Once a pharmaceutical company faces a quality failure, rebuilding consumer trust can take years, if not decades. Consumer confidence is essential in an industry that deals with public health.
The significance of pharmaceutical QA lies in its ability to prevent these issues, ensure the safety of patients, and ensure the longevity of pharmaceutical companies.
Types of Quality Assurance in the Pharmaceutical Industry
There are several types of QA systems and activities within the pharmaceutical quality management industry, including:
-
Good Manufacturing Practices (GMP) ensure that pharmaceutical products are consistently produced and controlled according to established quality standards. It includes guidelines for production, packaging, labeling, and storage.
-
Good Laboratory Practices (GLP) govern non-clinical laboratory studies and ensure that laboratory tests produce reliable and reproducible results. This is critical for drug development and ensuring that drugs are safe before clinical trials.
-
Risk Management: This QA process involves identifying, assessing, and mitigating risks that may impact the quality and safety of the pharmaceutical product.
-
Validation and Verification: These processes ensure that manufacturing equipment, processes, and systems perform as expected. Validation includes ensuring that procedures deliver the desired results while verification confirms that standards are met.
-
Internal Audits and Inspections: Regular internal audits are conducted to assess compliance with regulatory requirements and identify potential areas for improvement.
-
Supplier Quality Assurance: Ensuring that raw materials and components sourced from external suppliers meet quality standards is vital for maintaining the integrity of the pharmaceutical product.
Steps to Implement Quality Assurance in the Pharmaceutical Industry
Implementing QA in the pharmaceutical industry involves a series of steps, including:
-
Establishing Clear Policies: Create comprehensive QA policies that outline the company's quality standards, processes, and responsibilities.
-
Designing Quality Management Systems (QMS): Develop a robust QMS to document and manage all QA activities. A QMS helps organize quality-related tasks, audits, and corrective actions.
-
Training and Education: Equip all employees, especially those involved in production and testing, with the necessary training to understand quality requirements and standards.
-
Developing Standard Operating Procedures (SOPs): SOPs ensure consistency in activities' performance and meet quality standards at each stage.
-
Monitoring and Evaluation: Continuously monitor processes to identify deviations or quality issues. Regular evaluations help ensure that processes remain effective.
-
Corrective and Preventive Actions (CAPA): Implement CAPA protocols to address any issues that arise and prevent their recurrence. This is essential in maintaining long-term product quality.
-
Continuous Improvement: Pharmaceutical QA is an ongoing process. Companies must regularly assess their QA systems, identify areas for improvement, and take corrective actions as needed.
Difference Between Pharmaceutical Quality Assurance and Quality Control
While pharmaceutical Quality Assurance (QA) and Quality Control (QC) are both focused on product quality, they are distinct processes:
-
Quality Assurance (QA) is a proactive approach focused on preventing defects before they happen. It involves the entire system, including planning, designing, and managing processes, to ensure that quality standards are met.
-
Quality Control (QC): QC is reactive. It focuses on identifying defects or issues in finished products. QC involves testing and inspecting products to confirm they meet the required specifications.
QA ensures the processes are set up to produce quality products, while QC ensures that the final product meets quality standards.
Role of QMS Software in Supporting Pharmaceutical QA System
Quality Management Software (QMS) is pivotal in modern pharmaceutical QA processes. Qualityze offers a comprehensive EQMS suite that supports every aspect of pharmaceutical quality assurance. Some of the unique features of Qualityze EQMS include:
-
Centralized Documentation Management: Qualityze allows users to manage documents, protocols, and test results in a centralized system, reducing the chances of errors and omissions.
-
Automated Workflow Management: The software automates many of the manual tasks associated with QA, such as document approvals, audits, and inspections, ensuring faster and more efficient operations.
-
Compliance Tracking: Qualityze EQMS includes real-time tools to track regulatory compliance, ensuring that pharmaceutical companies meet global industry standards.
-
Risk Management: The system helps identify, assess, and mitigate risks through real-time data analysis, improving decision-making.
-
Audit and Inspection Management: Qualityze EQMS helps manage and document internal audits and inspections, ensuring companies meet GMP and GLP standards.
Conclusion
Mastering pharmaceutical quality assurance is a complex, ongoing challenge. However, with the right tools, such as Qualityze EQMS, pharmaceutical companies can streamline processes, enhance compliance, and maintain high product quality standards. The importance of QA in ensuring public health and safety cannot be overstated, making it essential for every pharmaceutical company to adopt effective quality management practices.
Share
The Start of Something Amazing.
Request Demo
Products
Industries