Explained: 8 Disciplines of Problem Solving for Improved Product Quality
Table of Content
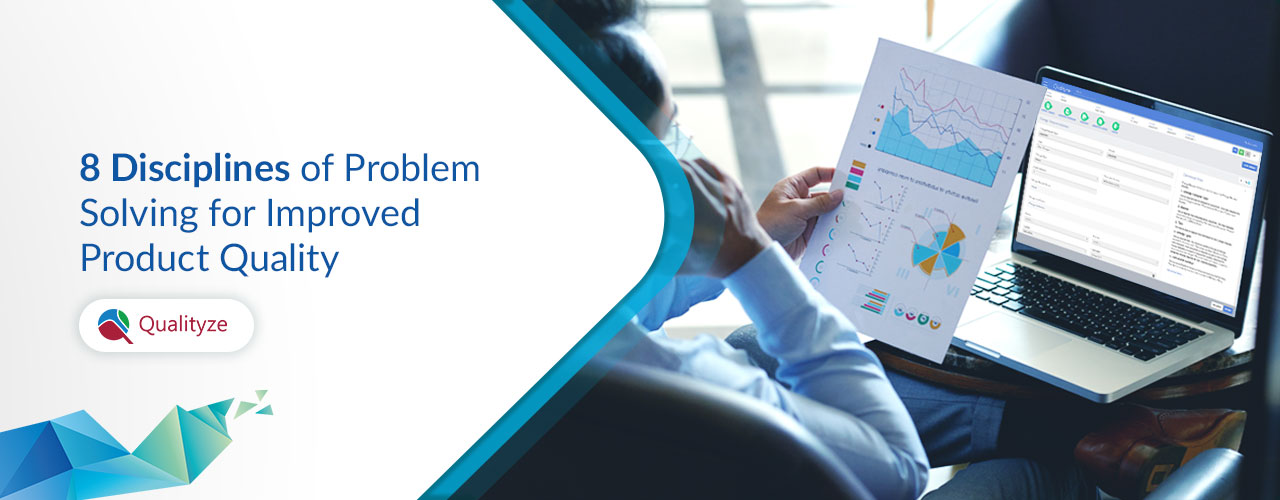
For manufacturers, it is quite common to encounter quality issues in products and services repeatedly. This may result in numerous problems. Some of them can be directly reported by customers while some may be identified by an internal audit team. In any case, quality issues may hamper the brand reputation and customer loyalty.
That’s the reason; the method of 8 disciplines was introduced to manage the quality issues by addressing their root cause and preventing the recurrence.
What Exactly is an 8D Problem-Solving Method?
8D is commonly referred to as “8 Disciplines” or “8 Critical Steps” for solving quality problems. It is a team-oriented method of managing quality issues, which is highly disciplined and effective. Based on the teamwork, this method offers stepwise guidelines to identify the root cause, define and implement the segregation actions, and finally develop and implement CAPA to mitigate the problem lastingly.
Benefits of Implementing 8D Problem-Solving Approach
8 Disciplines are an effective approach especially for manufacturers regardless of the industry they serve. It drives multiple benefits such as:
- Identification of real factors that led to the problem.
- Address the potential causes that could result in an undesirable situation or challenge.
- Allowing the team to perform a detailed analysis before making any conclusions.
- Preventing the recurrences of similar product and process quality issues.
Steps Involved in 8 Disciplines of Problem Solving for Improved Product Quality
D1: Team Building
You should create a separate team to resolve the quality issues and improve the overall implementation process. All the team members should be competent enough in terms of skills and knowledge to perform the duty assigned. In addition to the competency of the team, it is very important to understand the number of members required to efficiently manage the quality issues.
D2: Stating the Problem
Make sure you state all the details of a particular problem clearly and thoroughly to validate and verify the problem from all the possible resources including who, when, where, etc. It is also called the 5W2H methodology. It includes all the details like:
- (W)ho reported the problem?
- (W)hat is the actual problem?
- (W)hen exactly the problem started?
- (W)here it happened?
- (W)hy it is happening? (Complete Explanation Required)
- (H)ow often the problem has occurred? (To Understand the Pattern)
- (H)ow much quantity of products is affected?
Hence, stating the problem simply won’t work. You will have to describe it for creating and implementing an appropriate action plan.
D3: Define the Interim Containment Action
Once you have tracked all the details of the problem occurred, you need to identify the appropriate containment measures to prevent the problem from becoming continued adversity. The focus should be on the main issue rather than the symptoms. You can discontinue production, in case of defective products, to prevent any harm to customers.
D4: Determine the Root Cause
Kickstart the process by listing all the potential causes to determine the root cause of the problem. You can test and check every probability to identify the actual cause of the problem. Then, you can proceed to define the relevant corrective actions. The most commonly used method is 5M1E. These 6 elements are reevaluated every time a disturbance in the product quality is observed. The six elements are Man, Machine, Material, Method, Measurement, and Environment.
However, you can use multiple tools in the process of identifying the root cause of the problem. Some of the commonly used tools are Pareto Charts, Affinity Diagram, Brainstorming Session, 5-Whys Process, Fishbone Diagram, Fault Tree Analysis, Statistical Analysis, ANOVA, DOE, Regression Analysis, Hypothesis Testing, GR&R, Flow Charts, Audits, and FMEA.
D5: Define the Permanent Corrective Actions
Define the scope of improvements with a list of all the possible solutions. You must remember it is not about mitigating the issues for once; it is about implement the corrective actions that can resolve the issue permanently. You must focus on long-term corrective measures to avoid recurrences and other respective problems. Moreover, you should verify the improvements done if they are effective enough.
D6: Resolve the Issue and Perform Effectiveness Review
Once you have implemented the 5th Discipline and eliminated the root cause of the problem, verify the result. It will help you understand the effects of the solution implemented on the production processes. Remember that the effectiveness review is not a one-time activity; it should be an ongoing process to drive continuous improvement.
D7: Prevent the Recurrence and Standardize the Processes
The problem once resolved shouldn’t occur again and you have to ensure that in the Discipline 7. For this, you need to standardize all the processes, systems, and procedures. You can use a quality management software system to do standardization right. This will further help you to identify the changes required at every level or stage and maintain the continuous improvement cycle.
D8: Appreciate your Team
If all the disciplines are followed and implemented rigorously and you have noticed improvements, it’s time to appreciate your team for their sincere efforts. Also, plan the future activities in orientation with continual improvement to improve your business bottom line. Keeping your team involved makes them feel an important part of the process and they are likely to contribute best efforts.
Truth be told, the 8D process is quite an effective method than all other problem-solving methods. Implemented appropriately, all the process and problem-related quality issues can be easily implemented.
[Bonus Tip: Don’t keep appreciation discipline limited to say thanks to your team. Communicate with them openly to understand their needs whether they need any training or any other assistance to match the competency required to perform the jobs and duties assigned. It may work as a permanent corrective action as well.
You can also implement a training management system to manage their training needs effectively and efficiently. It is preferable to go for a cloud-based training software like Qualityze that offers them a flexible way of learning new skills regardless of the geographical locations they are placed at.
Besides all the important steps we have discussed above, you should know three important things about the 8D process and report that will be of great help in the long term.
- The 8D report is not for your customers. It is just for you to identify the root cause of a problem, resolve the same, and prevent the recurrence. Customers will evaluate everything with the quality delivered to them. However, you can keep and maintain the records to prove that you hear the customer complaints and concerns seriously and addressed them at earliest. It works as evidence for FDA visits.
- Implementing the 8D problem-solving approach is possible when the organization’s top management encourages it with complete authorization and commitment. On the other hand, the involvement of all other team members is equally important. Make sure you have established standardized quality management systems, processes, and procedures to bring the entire organization together to meet the business quality objectives.
- Always prepare a valid 8D report since it will help you improve the product quality and build more customer confidence in your brand. It is key to achieve customer satisfaction. Hence, record the entire process step-by-step to make most of the results you get.
Related Article: 7 Common Problems That Manufacturing Industries are Facing These Days
Hope this post has helped you understand the benefits of implementing the 8D problem-solving process for your business. You can automate and standardize this approach using Qualityze Enterprise Quality Management Suite.
If you want to know how our software can help, get in touch with our customer success team at info@qualityze.com or call us on 1-877-207-8616.
Share
The Start of Something Amazing.
Request Demo
Products
Industries