Table of Content
1 How you identify reliable suppliers?
2 Why is Supplier Quality Management Important?
3 Step-By-Step Approach: Makes Supplier Quality Management Successful
1. Selecting the right supplier for your business and industry-type
2. Creating and reviewing the approved supplier list
3. Auditing your supplier at regular intervals
4. Measuring supplier performance and generating their scorecards
5. Sharing timely feedback with supplier for improved quality
6. Tracking supplier performance for informed decision making
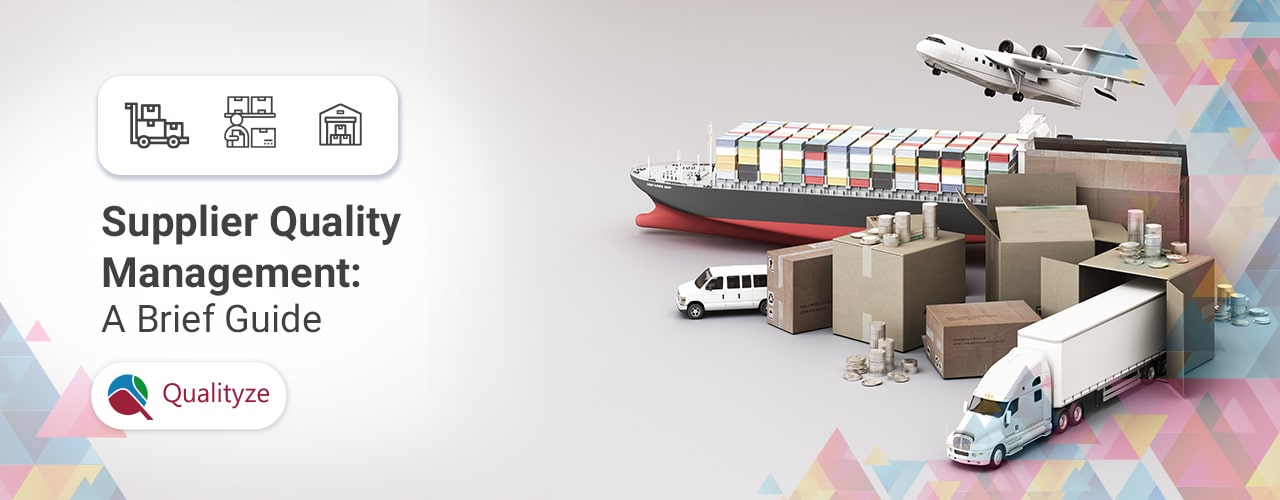
Even after being equipped with modern tools and equipment in the production unit, manufacturing businesses are concerned about reducing risks and avoiding costly production failures. It can happen due to poorly-managed processes, poorly maintained equipment and devices, periodic audits, and most important of all, flawed supplier management process – where it all begins.
Ensuring good quality output or products requires you to have the best quality raw materials and components. It is not practically feasible to check every single material, component, or part for quality. This is the reason; you need reliable suppliers for your business.
How you identify reliable suppliers?
Through the supplier qualification process! It is not as simple as it sounds. It requires you to document all the details related to suppliers like Supplier Name, Category, Site, Addresses, Contacts, Type, Certifications, and more. You can create your supplier onboarding questionnaire to verify whether the selected supplier meets all the criteria and requirements.
The next generation, cloud-based supplier quality management software comes with a pre-defined questionnaire that you can customize as per your internal and external specifications to streamline the supplier selection process.
Why is Supplier Quality Management Important?
Supplier quality management is imperative to manage critical functions such as managing supplier information, performance, and relationships. It enables any organization to:
- Improve Collaboration and Communication with Suppliers,
- Ensure consistent quality products,
- Strengthen business relationships,
- Deliver value to their customers,
- Gain operational excellence and competitive-edge, and much more.
Related Article : Know How Auditing Suppliers Help to Grow Your Business
Step-By-Step Approach: Makes Supplier Quality Management Successful
All enterprises need to develop a successful supplier quality management system is having a well-organized approach that includes the following steps:
1. Selecting the right supplier for your business and industry-type
Your business model and industry-type are different; so is the supplier-type for your business. You cannot just select the first supplier you find on the internet with minimum prices. Price is a thing that comes last. First and foremost is the quality of the products and services that the supplier delivers. In the online world of businesses where every other supplier promises to deliver quality, it can get daunting to pick the right one for your business.
Here’s the simple hack for it. Create a list of questions based on your business requirements to evaluate suppliers, including their market experience, clients they have worked for, location, and much more. It will make supplier selection easier for you.
2. Creating and reviewing the approved supplier list
Creating an approved supplier list helps you identify the suppliers that meet your organization’s selection and evaluation criteria. But you cannot keep it constant unless the suppliers continue to meet the requirements and pass the regular audits with flying colors. Reviewing the approved supplier list often helps you keep track of supplier performance and give them feedback, ensuring continuous improvements in the supplier quality.
Like audits, you can plan review for the approved supplier list regularly to grow and improve mutually, ensuring quality end-products for the customers without fail. It will significantly help improve your business-supplier relationship.
3. Auditing your supplier at regular intervals
If you want to stay ahead of ongoing supplier quality performance, you must have a streamlined supplier auditing process. The audits will help identify the supplier-related processes’ inconsistencies while enabling you to assess the supplier capabilities and make the supplier onboarding process easy and efficient. Planning and scheduling the supplier audits well-in-advance is preferred as best-practice to avoid any impact on the ongoing operations.
The best solution is integrated Supplier Quality Management Software that can help you efficiently manage audit criteria, schedule supplier audits, track and document results, and perform follow-up activities. It will help eliminate all the supplier defects and non-compliances quite systematically.
Related Article : Best-Practices for Supplier Quality Management That Are Worth Implementing
4. Measuring supplier performance and generating their scorecards
Measuring supplier performance is quite similar to the supplier selection process. It also requires you to have specific metrics defined for an error-free and unbiased evaluation of the suppliers associated with you for a long-time. The audits can be of great help here since they point out inconsistencies to investigate and determine the root cause. You can further generate supplier scorecards based on audit results and other performance criteria. It will ensure that you are associated with quality suppliers only who care for the business as much as you do.
With the right supplier quality management software, you can document all the supplier performance records as evidence of switching to another supplier. It demonstrates your organization’s commitment to best practices at the time of inspections and regulatory audits.
5. Sharing timely feedback with supplier for improved quality
Be it any business; constructive feedbacks help us all to improve and grow. It is equally essential for your suppliers to know what’s going well and what’s not to make necessary changes in their processes. It would be best if you will share feedbacks with suppliers at regular intervals. It will improve the quality of the product and strengthen your business relationships for the long-term.
The cloud-based supplier quality management software can help you collaborate and communicate with your suppliers quite often regarding the improvement required. You can also schedule follow-ups on the improvement activities using the advanced functionalities.
6. Tracking supplier performance for informed decision making
Keeping track of supplier performance is critical for informed decision making for your supplier onboarding process. You must have critical metrics to identify the fluctuations in supplier performance. You can also observe the patterns of downtime and uptime. It will help you make informed decisions to keep a supplier on board and provide them feedback for improvement or to end up the contract for continued poor performance over time.
Thanks to the advanced reporting and analytics feature of the supplier quality management software, it has become a lot easier and more efficient to track the supplier performance for any period and improve your decision-making ability. You can also guide your suppliers on the timeline their performance dripped all-time low so they can investigate at their level and improve accordingly.
Isn’t it an all-inclusive approach to perform the supplier quality management well? You can simplify it even more with the right Supplier Quality Management software like Qualityze that helps you track and manage the qualification process of new potential suppliers, maintain complete records of all suppliers evaluated on a centralized database, timely communication with all suppliers to provide feedbacks, manage approved supplier list (ASL), and manage supplier scorecard while seamlessly integrating with your existing ERP system.
Qualityze Supplier Quality Management enables organizations to streamline and standardize their supplier-related processes and mitigate operational challenges. Built on the Salesforce.com platform, it offers greater flexibility, security, and scalability to control and manage voluminous supplier records without any hassles.
A product’s quality starts at the supplier selection process as the suppliers play a vital role in bringing the product to the market. So, have you implemented a powerful supplier quality management system yet?
If not, the Qualityze customer success team can help. All you need to do is get in touch with us on 1-877-207-8616 or write to us at info@qualityze.com, and we will be right there for you. You can also request a free demo to get real-time insights into how the software works and make supplier quality management simple and straightforward.
Related Article : 5 Strategies for Supplier Quality Management that Actually Work
Share
The Start of Something Amazing.
Request Demo
Products
Industries