Table of Content
1 What is Medical Device Complaint Handling?
What does each regulatory framework do?
Bridging the Gap: Complaints vs. Feedback – What's the difference?
4 The Impact of Effective Complaint Handling on Medical Device Companies
5 Common Bottlenecks in Medical Device Complaint Management
6 Medical Device Complaint Handling Process
7 Steps to Streamline Medical Device Complaint Management:
8 The Strategic Role of Qualityze QMS in Medical Device Complaint Handling: Beyond Basic Compliance
Medical Device Complaint Handling - Precision in Process
Elevating Medical Device Quality Through Strategic Complaint Management
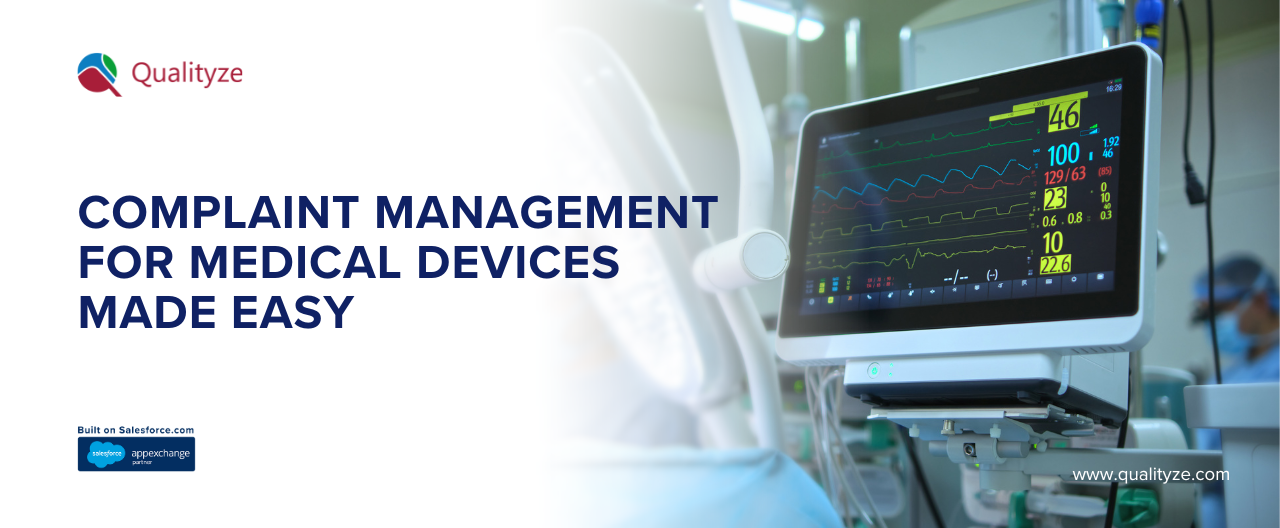
Handling complaints of medical devices is essential for maintaining compliance with FDA and ISO standards. Is your organization implementing the best practices?
Customer complaints are inevitable for any business enterprise. The medical science industry successfully manages dissatisfied clients so that they are impressed with the services offered by them.
The medical device sector is going to experience numerous changes in the next few years. Amidst fulfilling new regulations and guidelines, how can this sector keep pace with existing trends in technology?
Most FDA-regulated companies lack the processes or resources to handle product complaints efficiently. When the resulting backlog isn't addressed quickly and thoroughly, the problem snowballs into major safety and compliance issues that take dozens of hours of work to correct.
Join us in revealing the essentials of medical device complaint handling—from understanding regulatory compliance awareness to implementing an effective, automated complaint resolution system.
To build a strong foundation, we go ahead and explore the fundamentals of complaint handling and then take a deep dive into optimizing the process.
Definition of Complaint
According to FDA 820.3(b):
Complaint means any written, electronic, or oral communication that alleges deficiencies related to the identity, quality, durability, reliability, safety, effectiveness, or performance of a device after it is released for distribution.
What is Medical Device Complaint Handling?
Medical device complaint handling refers to a process of receiving, investigating, resolving, and documenting customer complaints related to medical devices. An important role made to ensure that any product defects are resolved immediately and in accordance with industry regulations.
Regulatory bodies, such as the FDA (21 CFR Part 820.198) and ISO 13485:2016, emphasize the need for medical device manufacturers to implement an effective complaint management system in place to identify product failure, ensure corrective action, and avoid repeatative occurrences.
What does each regulatory framework do?
-
FDA (21 CFR Part 820.198) – Mandates the manufacturers to establish a structured complaint-handling process in place.
-
ISO 13485:2016 – Requires a documented process of complaint handling and regulatory reporting.
-
EU MDR (Medical Device Regulation) – Guarantees post-market surveillance and complaint management.
Did you know? Automation of complaint handling process can help reduce processing time by up to 50%.
Bridging the Gap: Complaints vs. Feedback – What's the difference?
Both complaints and feedback are useful sources of information, having different objectives. Complaints point out specific problems that need to be addressed immediately, while feedback gives a more general view of areas for improvement.
This differentiation is important in assisting medical device companies have better complaint-handling practices, which help them comply better and produce excellent products.
Let's see how a formal complaint management process benefits medical device businesses...
The Impact of Effective Complaint Handling on Medical Device Companies
Effective complaint handling is not merely a regulatory necessity—it is a primary driver of product quality, patient safety, and brand reputation.
Fundamentally, it has a direct impact on patient safety and trust. Prompt and comprehensive resolution of complaints shows a commitment to care and quality, avoiding potential harm and building confidence.
Regulatory compliance is a critical aspect of complaint handling. Non-compliance may result in serious consequences, such as large fines, product recall, and legal action, all of which can severely affect a company's financial status and reputation.
Brand reputation is now more exposed than ever in this era of digitalized society, with social media and online feedback spreading word-of-mouth faster than ever. One badly managed complaint can easily spiral out of control, damaging a company's reputation and damaging customer trust.
On the other hand, an active and effective complaint-handling system increases customer satisfaction, promotes brand loyalty, and generates positive word-of-mouth. In addition, complaint data analysis offers important information for product improvement. Through the identification of repeating problems and patterns, companies are able to prevent potential defects proactively, improve product quality, and pursue ongoing improvement.
A statistical fact! Medical device firms with structured complaint handling decrease recall risk by as much as 60%.
Common Bottlenecks in Medical Device Complaint Management
Many medical device companies encounter common bottlenecks in their complaint management processes. Despite its importance, medical device complaint management comes with several challenges:
-
Lack of a Standardized Process
Without a structured approach, complaint resolution becomes inconsistent and inefficient.
-
Manual Processes and Data Silos:
Insufficient centralized data slows trend analysis and reporting to inefficiency, error, and delay in complaint processing
-
Inefficient Tracking & Documentation
Companies using manual complaint management struggle with compliance and audit readiness.
-
Compliance Challenges
Constant updates in regulatory guidelines require companies to frequently adapt their processes.
-
Delayed Response Times
Prolonged investigations and resolution processes cause patient dissatisfaction and increase the potential for regulatory scrutiny.
-
Inadequate Documentation and Reporting
Inaccurate records hinder the ability to prove compliance in audits and investigations, resulting in regulatory penalties and legal challenges.
Medical Device Complaint Handling Process
Medical device complaint handling process generally follows some important steps. Complaints are first received from different modes of communication like phone, mail, or web forms and preliminary evaluation is conducted in order to find out their priority and urgency. Triaging and prioritizing are essential at this stage. Then an extensive investigation is done to realize the root cause of the defect.
Tools like the 5 Whys and Fishbone diagrams can be used to identify underlying problems systematically. Corrective and preventive actions (CAPA) are subsequently applied to correct the root cause and prevent future occurrences.
Verification of the success of these actions is necessary. Extensive documentation and reporting are necessary for monitoring and proving compliance. Proper and timely records of all actions and results must be kept.
Lastly, the complaint is closed, and follow-up steps are followed to make sure the issue is resolved to the customer's satisfaction. Customer satisfaction surveys and communication can be employed to measure effectiveness
Did you know? Automation of complaint handling can reduce processing time by up to 50%. Source: Gartner
Steps to Streamline Medical Device Complaint Management:
In the pursuit of operational excellence and regulatory compliance, medical device companies must proactively streamline their complaint management processes. How is this done? Streamlining complaint management for medical devices, companies implement a centralized Quality Management System (QMS).
Here are key steps to achieve this transformation:
-
Implementing a Centralized QMS:
Use a strong Quality Management System (QMS) such as Qualityze's Quality Management System. This integrates complaint management with other critical quality processes, such as CAPA, document control, and audit management, creating a unified platform for efficient data management and process control. A centralized QMS breaks down data silos and ensures smooth information flow.
-
Automating Workflows and Notifications:
Leverage automation capabilities in your QMS to streamline complaint handling workflows. Implement automated notifications to notify relevant personnel about new complaints, investigation updates, and CAPA tasks. This MINIMIZES manual work, minimizes delays, and ensures timely action. Qualityze's CAPA Management Software can be utilized together with complaint management for automated workflows.
-
Standardizing Complaint Handling Procedures:
Implement and maintain Standard Operating Procedures (SOPs) to provide detailed guidelines for receiving, investigating, and complaint resolution. Ensure training for all staff on such procedures to ensure compliance and consistency. Qualityze's Document Management Software assists in maintaining SOPs.
-
Enhancing Data Visibility and Reporting:
Leverage real-time dashboards and analytics in your QMS to gain insights into complaint patterns and trends. Qualityze /assists in maintaining records that can be utilized for reporting. This allows proactive identification of potential issues and facilitates data-driven decision-making.
-
Providing Comprehensive Training:
Implement frequent training programs that familiarize the staff with requirements from regulations, procedures for addressing complaints, as well as standard procedures. Complement the workforce with the understanding and expertise it requires to accomplish tasks effectively through handling complaints. Training and supporting all of their products is an offer made by Qualityze too.
Implementing these strategic steps, medical device companies can significantly enhance their complaint management processes.
The Strategic Role of Qualityze QMS in Medical Device Complaint Handling: Beyond Basic Compliance
In the complex landscape of medical device complaint management, a generic QMS falls short. Medical Device Complaint Handling needs medical grade precision where brands like Qualityze's platform is engineered to transform complaint handling from a reactive necessity to a proactive strategic advantage.
Seamlessly incorporating complaint data into the center of a quality system, enabling real-time trend identification and predictive analytics is the way to address such complaints. Utilizing Qualityze's powerful analytics, organizations are able to discover nascent problems prior to them worsening, minimizing risks and enabling compliance sustainability.
Automated CAPA workflows on the platform are not simply tracking actions; they're about enforcing fast, validated resolutions. Qualityze's ensures that each complaint, investigation, and CAPA is thoroughly documented and available. This offers an end-to-end audit trail that makes regulatory submissions and inspections easier.
Key among these is the closed-loop process of Qualityze, which means that complaint data directly feeds product and process optimization, establishing an ongoing cycle of quality improvement. This integration and forward-looking control are what make Qualityze different, allowing medical device manufacturers not only to meet but to surpass regulatory requirements and patient safety regulations.
Medical Device Complaint Handling - Precision in Process
When it comes to medical device quality, complaint handling is a powerful tool for guaranteeing compliance with regulations and protecting patient safety. Effective complaint handling is dependent upon an extremely well-defined, risk-based process. Below are the most critical stages, based on industry best practice and regulatory requirements:
-
Complaint Receipt and Triage (Initial Assessment):
Once received, every complaint is immediately triggered. This includes categorization of the complaint by severity, risk potential, and reporting requirements per regulation (e.g., MDR). This process uses risk assessment matrices to prioritize issues that are urgent, in accordance with FDA recommendations for timely reporting.
-
Investigation and Root Cause Analysis (RCA):
An organized probe follows, utilizing methods such as 5 Whys or Fishbone diagrams. The goal is to pinpoint the ultimate root cause, not mere surface symptoms. This step requires cross-functional involvement, including quality, engineering, and clinical staff, to maintain comprehensiveness.
-
Corrective and Preventive Action (CAPA) Implementation:
Based on the RCA, CAPA plans are developed and executed. Not just the current issue is addressed but future issues as well are prevented. Objective evidence like test data or process validation ensures that CAPA works and is implemented in accordance with ISO 13485 standards.
-
Documentation and Record-Keeping:
Comprehensive documentation is maintained throughout the process. This includes complaint details, investigation findings, CAPA plans, verification results, and closure justifications. Such specificity is needed for audits and signifies compliance with 21 CFR Part 820.
-
Complaint Closure and Post-Market Surveillance:
Once CAPA effectiveness is confirmed, the complaint is closed. Post-market surveillance activities, including trend analysis and feedback loops, are then implemented to monitor for recurring issues and identify potential improvements, thus creating a closed loop system.
Elevating Medical Device Quality Through Strategic Complaint Management
In the complex medical device manufacturing industry, complaint management is not just a regulatory necessity—it is a strategic necessity for patient safety and brand resilience. By adopting a well-disciplined process, leveraging robust QMS solutions, and emphasizing continuous improvement, organizations can transform potential vulnerabilities into success drivers.
To actually manage the nuances of modern medical device conformity, look towards a solution that integrates and automates the end-to-end complaint handling process. Qualityze delivers an end-to-end QMS that is suited to the singular requirements of the medical device world and offers real-time visibility into your processes alongside optimized workflows.
Ready to feel the difference? Find out how Qualityze's Complaint Management Software can transform your complaint handling process and maintain regulatory compliance.
Book a customized demo now and begin on the path of operational excellence
Simplifying operational processes means amplifying your impact. Move beyond reactive responses. Effective complaint management is the foundation of proactive quality!
Share
The Start of Something Amazing.
Request Demo
Products
Industries