Table of Content
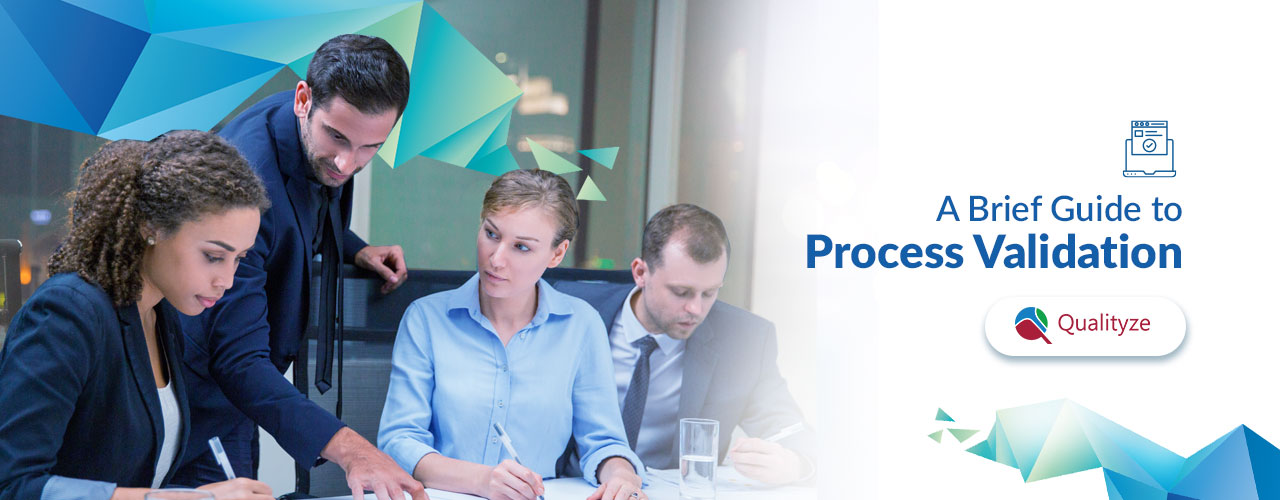
Since there has been a huge buzz around the term Process Validation, it has become critical to understand the philosophy of this term. Some organizations set some rules to achieve validation. It’s not the right way to go about it.
Process Validation refers to knowing a process thoroughly and approaching the same in a structured way. It involves ultra-careful Documentation for every step, including manufacturing, device history, SOPs, and other controlled documents. If the process validation is not conducted, you will eventually be producing a poor-quality product.
Especially in the Food and Beverage industry, the process validation should be taken quite seriously since the products they make is consumed by people in different quantity. A compromise on quality can turn into a frightening health risk.
This post will help you understand the general principles and approaches outlined by the FDA for the process validation in manufacturing different types of products. FDA emphasizes on the use of newer development concepts, risk management, and other quality systems based on the stages of the product lifecycle.
Firstly, let’s understand the difference between process validation and verification since these are interchangeably used terms
Process Verification is examining and evaluating a product’s functionality against some specified requirements supported by objective evidence. In this process, product conformance is checked against the defined requirements.
On the other hand, Process Validation is keeping a check on the flow of process through objective evidence to ensure consistency in products as well as processes. It helps you to prove that your processes or equipment are producing good results.
Related Article : How Cloud QMS Simplifies Process Validation
Let’s look at FDA guidelines for Process Validation:
We all know that FDA guidelines are defined to ensure the highest degree of quality in a product by meeting all the attributes and requirements they are intended for.
General Considerations for Validation as defined by the FDA:
A product lifecycle comprises different stages that need to be recorded and stored to make the process validation more effective. There are multiple practices that will help you to collect necessary information about the processes. Such information can help in improving the product lifecycle in the later stages. Here are the general considerations for process validation highlighted by the FDA:
- They recommend a collaborative approach to process validation. It requires the support of experts from different disciplines and top management. It is an essential aspect to achieve success as we all know, “Everyone is Responsible for Quality.”
- They recommend a streamlined and standardized procedure to conduct research, initiate training programs, manage risks, etc. All the relevant information should be formally recorded and approved based on the established processes for the different stages of the product lifecycle.
- They recommend not to use the terms – attributes and parameters to define the criticality of a process. For a progressive approach to process validation, manufacturers must take risk management as a sequential process than a one-time process since the entire concept revolves around risk-based decision making. The manufacturers should evaluate the attributes and parameters based on their contribution to the process and the changes they bring to the product or the material used in the product. All such information should be revaluated wherever the new lot of information is accessible. Also, the quality controls of these attributes or parameters should be directly proportional to the degree of risks they possess for the process and its output. In simple words, keep the degree of control higher for the attributes or parameters that can be of higher risks. However, the terminology may vary from one manufacturer to other. The only condition is that they should clearly define their terminologies and categorizations to avoid any severe troubles.
- They recommend maintaining the consistency of the processes and controls to achieve the objectives of process validation steps since many products may have a complicated process or have a single-source dependency. Through validation, a process should be assured against all odd situations that could lead to hampered production output, supply-chain variances, and can be harmful to public health. FDA has outlined three recommended stages for the process validation, including:
Stage 1: Process Design
The very first stage of the process validation is all about defining the processes that will be followed in the product lifecycle. The main objective is to design the entire process that can be used regularly for consistent product quality that conforms to all the stated requirements. It can be further categorized into information gathering and strategizing the process controls to define the operational limits.
Only then you can look forward to the next step.
Stage 2: Process Qualification
In this step of Process Validation, the process design formulated in the first step is examined and evaluated against reproducible manufacturing. It can also be categorized into two steps: firstly, designing the facilities (such as equipment and utilities) while defining their qualification, and secondly, illustrating the process performance qualification to ensure that only trained professionals and qualified equipment are used.
Stage 3: Continued Process Verification
In the final step of process validation, it’s all about the assurance that the process defined is under control during the product lifecycle. It must have a system to identify the variances that can obstruct you from attaining the quality objectives within the specified time. It can also be referred to as the maintenance stage, where you need to keep a check on process and equipment qualification to avoid quality issues and unnecessary delays.
Make sure you manage the maintenance and calibration frequency based on the data gathered in the verification phase to minimize the operational efforts and costs.
Even after releasing so many guidelines and assistance for the Process Validation, FDA found many organizations missing out on the most crucial component i.e., Documentation.
Documentation should be maintained for every stage, especially for complicated projects. It’s of high prominence to make the relevant information accessible to all the people involved in a product lifecycle. Such structured systems for capturing the information help organizations to make well-informed decisions based on the data being tracked and trend.
Also, documentation part of the process may vary for all three stages, including Process Design, Process Qualification, and Continued Process Verification. It also serves purposes like process improvements, redefining the processes, and much more.
Process Validation will be very tough to conduct with manual intervention. The best way to manage this complex process is by implementing a powerful and secure quality management system like Qualityze. It will help you to manage all the things related to process validation, including documentation to comply with the FDA guidelines.
Qualityze EQMS Suite helps you manage all the stages of process validation in a standardized manner to ensure consistency. It comes with amazing in-built capabilities and features. The user-friendly interface and scalable Salesforce platform make Qualityze Quality Management software perfectly suitable for modern businesses with ever-growing and changing landscapes.
To experience the Qualityze difference in real-time, you can request a demo now. You can also get in touch with our customer success team for more insights and get all your product related queries resolved.
Share
The Start of Something Amazing.
Request Demo
Products
Industries