Table of Content
1 Market Drivers for Quality Management
2 Challenges of Disconnected Quality Systems
3 Importance of Closed-Loop Quality Management
4 The Role of AI-Powered CAPA Software
5 Key Benefits of AI-Powered CAPA Systems
6 Steps for Successful Deployment of AI-Powered CAPA
7 Measuring Success with Key Performance Indicators (KPIs)
8 The Need for an AI-Powered CAPA Solution
9 Qualityze AI-Powered CAPA Solution: The Future of Quality Management
10 The Final Note
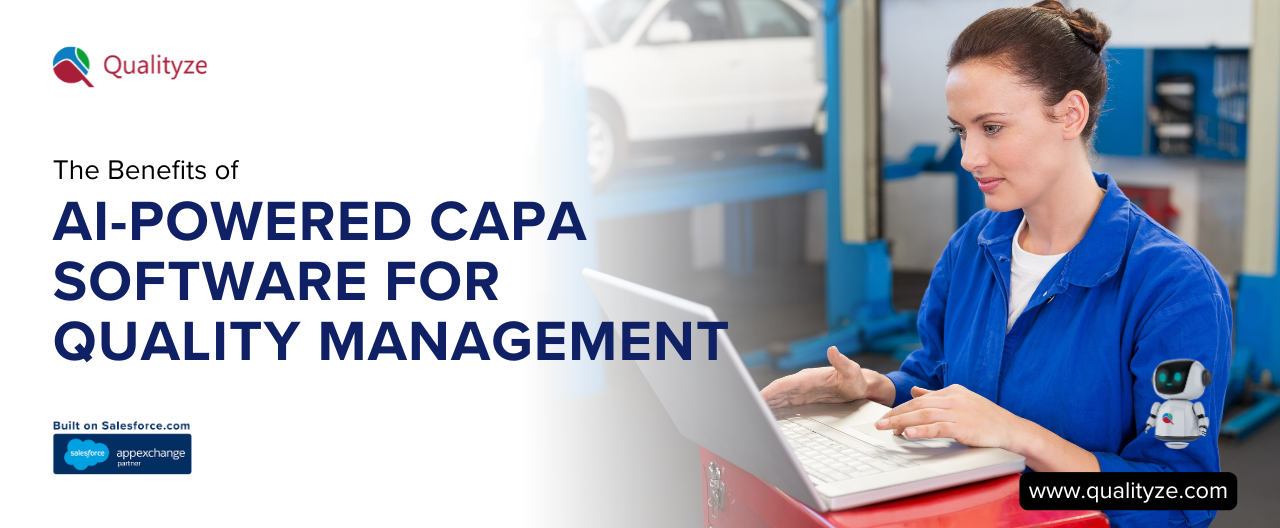
For manufacturers in industries like automotive, aerospace, electronics, and medical devices, effective quality management is crucial to staying competitive. These industries explicitly deal with complex products, and the market evolves rapidly, making quality a key differentiator for success. Qualityze AI-powered Corrective and Preventive Action (CAPA) software helps companies tackle these challenges head-on.
Through this blog, we will understand the role of AI-powered CAPA in managing quality effectively. Also, we will find out how it helps reduce costs, improve processes, and drive proactive decision-making.
Market Drivers for Quality Management
Today, manufacturers have a lot of pressure to make high-quality products while keeping costs low. Some important reasons include:
- Customer-Centric Models: Companies are focusing more on customer experience, which means they need to keep an eye on quality in real-time and fix problems quickly. Even small quality issues can affect customer satisfaction a lot.
- Pressure to Reduce Costs: Reducing the cost of quality is very important for companies in industries like Medical Devices, Pharma, and General manufacturing. Better quality processes help reduce rework and avoid expensive mistakes.
- Need for Faster Response to Quality Problems: In today's connected world, companies need to fix quality problems quickly, no matter where they happen. AI-powered CAPA solution can help manage quality effectively and efficiently
Challenges of Disconnected Quality Systems
One of the biggest problems manufacturers face is managing quality with systems that don't connect well with each other. These disconnected systems can lead to:
- Longer Time to Fix Problems: Without a central quality system, fixing problems takes longer, which affects productivity and customer satisfaction.
- More Rework and Repeat Issues: When quality data is spread out, it's harder to find the root cause for problems, which means issues will happen frequently and more rework is needed.
- Higher Risks: Poor visibility among departments increases the risk of missing quality problems in time.
Disconnected systems make it hard for companies to keep quality consistent. To solve these issues, manufacturers need a connected quality management approach.
Importance of Closed-Loop Quality Management
To manage quality well, manufacturers need a closed-loop quality management system. This means connecting all quality processes from start to finish—from design to production to customer delivery. A closed-loop system makes sure that quality issues are found, analyzed, and fixed at every stage.
By connecting different departments like engineering, production, and service, companies can stop quality problems from happening again and keep improving products and processes. This approach helps lower quality costs while improving efficiency and customer satisfaction.
The Role of AI-Powered CAPA Software
AI-powered CAPA software makes closed-loop quality management even better by using advanced technologies that help with predictive and data-driven decision-making. Here are some key benefits:
- Better Root Cause Analysis: AI can find patterns in quality data that might not be easy to see, which helps find root causes faster and more accurately.
- Predictive Quality Management: AI helps manufacturers predict quality issues before they happen, allowing them to take action to prevent costly mistakes.
- Automated Decision-Making: AI-powered CAPA systems can make routine decisions automatically, reducing the workload for quality teams and ensuring consistent actions.
The AI-powered approach helps create a smooth flow of data and processes, making sure quality management is always proactive, connected, and improving.
Key Benefits of AI-Powered CAPA Systems
An AI-powered CAPA system offers several key benefits that help manufacturers enhance quality and reduce costs:
- Reduced Cost of Quality: By identifying and addressing potential quality issues in the design or production phases, manufacturers can significantly reduce the cost of quality.
- Improved Collaboration: Centralized quality data enables engineering, production, and supplier teams to work more effectively, ensuring quality standards are upheld across the entire product lifecycle.
- Real-Time Insights: AI-powered CAPA systems provide real-time visibility into quality performance, helping teams take immediate action and preventing issues from escalating.
- Automation Capabilities: AI-driven CAPA systems automate key quality processes, such as Non-Conformance Management and Risk Management, making compliance simpler and reducing risk.
By leveraging AI-powered CAPA systems, manufacturers can ensure that quality is embedded throughout the product lifecycle, from concept to customer delivery.
Steps for Successful Deployment of AI-Powered CAPA
Setting up an enterprise-wide AI-powered CAPA system requires a well-coordinated approach involving people, processes, and technology:
- People: Leadership must prioritize quality, and cross-functional teams should be engaged to ensure collective responsibility for quality.
- Processes: Standardize CAPA procedures across the organization to promote consistency and efficiency. Ensure that issues are captured and addressed at every stage of the product lifecycle.
- Technology: Integrate AI-powered CAPA with existing core systems to create a cohesive environment that facilitates collaboration and enhances communication across the value chain.
By aligning these resources, manufacturers can successfully implement AI-powered CAPA and drive continuous quality improvement.
Measuring Success with Key Performance Indicators (KPIs)
To track the effectiveness of an AI-powered CAPA system, manufacturers should establish key performance indicators (KPIs) that evaluate quality processes:
- Cost of Quality: This KPI tracks prevention, inspection, and failure costs to ensure efficient use of resources.
- First Pass Yield: This measures the efficiency of production processes in delivering quality products without rework.
- Successful New Product Introductions (NPI): This KPI assesses how well new products meet quality standards and minimize production-related issues.
Tracking and analyzing these metrics helps manufacturers identify areas for improvement and optimize quality processes.
The Need for an AI-Powered CAPA Solution
As products and processes become more complex, traditional CAPA systems may fall short of meeting evolving quality requirements. Qualityze AI-powered CAPA solutions provide the agility and intelligence manufacturers need to stay ahead of challenges:
- Enhanced Root Cause Analysis: AI can identify hidden patterns in quality data, enabling faster, more accurate root cause identification.
- Predictive Insights: AI-powered systems predict potential quality issues, allowing manufacturers to proactively prevent problems before they escalate.
- Automated Responses: AI-powered CAPA systems automate quality decisions, ensuring consistent responses and reducing the burden on quality teams.
AI-powered CAPA solutions provide the next level of quality management, empowering manufacturers to drive continuous improvement, reduce risks, and deliver products that meet and exceed customer expectations.
Qualityze AI-Powered CAPA Solution: The Future of Quality Management
At Qualityze, we offer a comprehensive AI-powered CAPA solution that helps manufacturers simplify quality processes, improve collaboration, and ensure compliance throughout the value chain. Our solution integrates seamlessly with existing core systems, allowing you to:
- Automate Corrective and Preventive Actions: Qualityze CAPA automates the entire CAPA process, from identifying issues to analyzing root causes and implementing corrective actions, performing effectiveness reviews, saving time and resources.
- Advanced Built-In Tools: Qualityze offers advanced built-in tools like 5 Whys, 5 How’s, and more tools for detailed investigation for every CAPA reported. This enables you to detect the root cause(s) of the problem so you can mitigate the issues and prevent their reoccurrence.
- Centralize Quality Data: Qualityze ensures that all quality data is consolidated, enabling informed decision-making and reducing communication gaps.
- Gain Real-Time Visibility: Our solution provides real-time insights into quality performance, enabling early issue detection and proactive action to prevent recurrence.
- Improve Collaboration: Qualityze enables different teams to collaborate effectively on quality issues, ensuring that corrective actions are communicated and implemented efficiently.
By leveraging the Qualityze AI-powered CAPA solution, manufacturers can create a connected and proactive quality management environment that supports continuous improvement and operational excellence.
The Final Note
AI-powered CAPA software is a powerful solution for manufacturers to overcome the challenges of disconnected quality systems. It provides a connected and intelligent approach to quality management, empowering manufacturers to identify issues early, reduce costs, and drive continuous improvement to meet and exceed customer expectations.
Gain control of your quality management processes with AI-powered CAPA Management Solution.
Share
The Start of Something Amazing.
Request Demo
Products
Industries