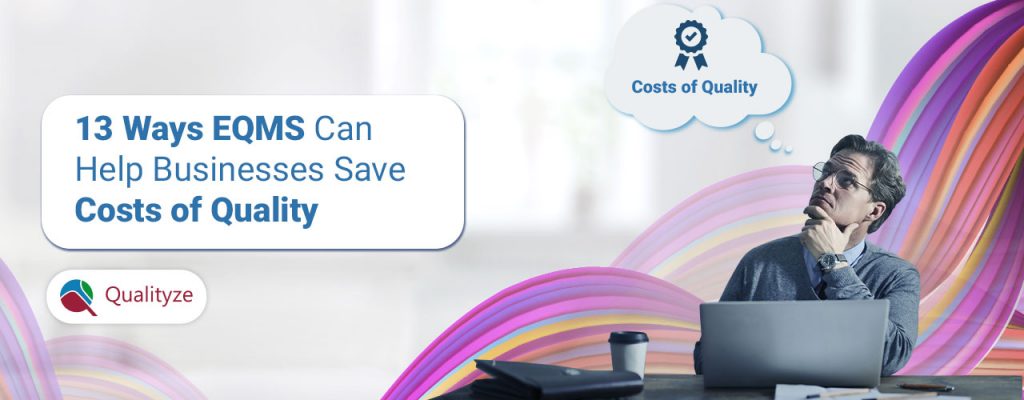
Managing quality is not just about reduced defects, deviations, and nonconformances. It is about the holistic approach to quality management and saves costs of quality wherein an organization evaluates every aspect from the process management to equipment calibration, supplier selection to material inspection, employee training to customer satisfaction, and identifying the ways to achieve quality, operational excellence, and compliance.
For a holistic approach, organizations need a powerful quality management system to evaluate and improve the overall processes, procedures, and systems. A QMS offers better quality control and streamlines production cycles by standardizing the quality processes. It helps unleash the maximum potential of the quality data collected and processed on a centralized platform to continuously make informed decisions, enabling organizations to continuously improve product and process quality. It also helps in achieving compliance with the applicable regulatory standards.
Another benefit you can have by implementing a quality management system is reduced quality costs. However, there are different ways a QMS helps in reducing costs and overhead expenses. We will look at 13 effective ways in this post.
1. It Standardizes the Change Implementation Cycles
One of the most common yet complex process that organizations struggle to strike a balance is change management. Despite so much discussion around the benefits of embracing change, many organizations do not have a streamlined change management process. Such organizations look at the change as a disturbance for ongoing operations. That’s where they fail at creating a culture of quality and continuous improvement.
An effective quality management software helps organizations streamline and standardize their change management processes to drive quality improvements most subtly without affecting the ongoing operations and overall organizational productivity. A QMS allows you to embrace every aspect of change that gives your business a competitive advantage over others.
In addition to the competitive edge, you are likely to save huge costs on resources required in traditional change management processes.
2. It Fosters an Environment of Learning
With the processes becoming more sophisticated and more stringent, organizations need to emphasize employee training and learning for improved performance. The traditional means of training are neither effective nor reliant when meeting ever-changing and growing customer requirements. It implies a need for an integrated training management system that can help organizations to fill the skill gap, making their employees competent for the job/tasks assigned.
A comprehensive quality management software can serve the purpose quite prominently and help organizations increase their workforce competency by streamlining the training processes. An EQMS suite, on integration with training management systems, can foster an environment of learning with flexible training programs for your employees, based on the job-function and department.
Therefore, you are likely to save costs of infrastructure and training materials that you used to bear
3. It Streamlines the Equipment Calibration
Organizations must take good care of equipment, instruments, and other devices to ensure excellent and consistent quality outcomes. For which, they need to streamline their equipment’s calibration and maintenance activities. An integrated quality management software helps create a closed-loop quality system to efficiently manage the process, product, supplier, and equipment quality.
An EQMS helps document, track, and verify the equipment calibrations with their outcomes, demonstrating your organization’s commitment to best practices. Keeping the calibration details and certificates documented also helps meet compliance. The quality management system also gives better control to your quality managers by increasing the traceability of the tools that are due for calibration. It ensures that all the devices are within tolerance levels against the standard values defined.
Lesser will be measurement differences; lesser will be the product quality issues. Hence, you will save huge costs on product rework and recalls.
4. It Reduces the Inspection Pressure
Most companies are now preferring to reduce the pressure on inspection by handing over inspection to the production people, leaving minimal dependency on the inspection process for quality. A quality management system enables you to experiment with different types of strategies to make this move successful.
A quality management solution often helps you streamline inspection processes, based on the different aspects; for example, if there is a change in design or change in the manufacturing sources, you can simplify the inspection process in alignment with production process validation so that the change doesn’t impact the form, fit, and function of the product.
A QMS not only reduces the efforts and process cycle time for managing change; it also significantly reduces the cost of additional resources required to drive change and inspection processes the traditional way. Experience the easiest and straightforward way to handle inspection pressure with a quality management software that comes with a cost advantage.
Related Article - Automating These Processes Can Reduce Cost of Poor Quality
5. It Automates the Quality Processes
Managing quality processes manually is time-consuming and tedious, especially in this rapidly evolving era of technology. Every organization needs to manage multiple functions, including CAPA, Change, Complaints, Calibration, and more, to ensure consistent product quality while embracing the continuous improvements on the go. It implies chaos of processes that can no longer be managed manually.
A quality management software solution helps streamline and automate the quality processes, reduce cycle time, and ensure faster time-to-market. It gives your quality team more control and confidence in managing the critical processes while achieving operational and compliance excellence.
Automating the quality processes reduces the chances of errors and frequency of customer complaints to protect your brand reputation, which can cost you the business.
6. It Offers Greater Control of Processes
Process control is essential to ensure the organization’s operational excellence, which increases profitability, provides quality, and ensures safety. Proper process controls are necessary to maintain product quality. But they cannot be managed to utilize traditional tools and techniques anymore.
Quality management software is the need of the hour. It helps organizations to ensure process controls in place to avoid quality failures. Process controls allow control errors that could lead to a catastrophic event or life risk. A QMS creates a closed-loop system of quality processes with proper authorities at every production stage, ensuring superior product quality every time.
There will be fewer errors and failures; you will be spending lesser money to fix the same.
7. It Improves the Supplier Relationships
The organization depends on the suppliers for the critical assemblies. They need enough time to evaluate the suppliers on different criteria to create their approved supplier list to assign essential jobs without worrying. Supplier selection done right helps ensure the required attention is given in every product’s case. There are many other concerns associated with supplier selection, including costs, efficiency, timeliness, and more that cannot be managed with traditional spreadsheets.
A powerful quality management software is required that can help manage the supplier-related processes as efficiently as other processes. It enables organizations to improve collaboration and communication with the suppliers, encouraging them for better performance.
Supplier-related processes managed right reduces the risks involved while lowering the cost incurred due to inferior quality materials.
8. It Reduces the Costs of Quality Failures
The costs of quality failures often lead to more significant troubles for the organizations, including increased costs and a threat to the reputation. It cannot be managed using the traditional reactive approach to risks wherein you spend more on the issue. It’s high time for organizations to take a proactive approach as well. It will help prevent the quality issue before it leads to any unfortunate event.
A quality management solution enables organizations to take a proactive approach to risk management while keeping them prepared with a reactive approach, too, for unexpected events.
9. It Reduces the Documentation Costs
Whether you want to file a nonconformance report or wish to update new versions of the document, the traditional document management system will burden you with massive costs. Moreover, you will face the visibility and traceability issues due to dispersed data.
The advanced quality management software seamlessly integrates with the cloud-based document management software to manage all the documentation related tasks from creation to approval, version control to publishing, and making it obsolete. It also improves the quality data’s visibility and traceability, allowing organizations to meet compliance with eSignature validation.
Therefore, you can save a considerable amount of costs for managing documents in a paperless, hassle-free, and timely manner.
10. It Improves Task Routing
The costs of routing the critical tasks are quite underrated in the organizations. For example, – you have created a workflow process across multiple departments. And, it involves all the members in every phase/discrepancy. It will impact the productivity of the people who are not even needed.
Quality management software helps configure the process workflow while limiting the participants in each discrepancy according to the need, by adjusting the workflows for different types of issues with different escalation process, ensuring the best use of your team members’ time.
11. It Manages the Redundant Tasks Efficiently
Organizations often invest time, resources, and costs in managing repetitive tasks. They need to streamline such tasks to reduce the process cycle time and increase the cost-effectiveness. The best solution is compliance-driven quality management software.
An Enterprise Quality Management Solution helps meet your quality, compliance, and regulatory requirements by leveraging Industry best practices with standardized, repeatable processes through easy-to-configure predefined workflow templates. The cloud-based quality systems generally possess an integrated design that connects all the QMS processes for a complete solution.
Isn’t QMS a simplified and straightforward approach to quality and compliance management within minimal costs.
Related Article : Quality Culture: A Comparison of Costs
12. It Helps Managing Reworks Effectively
Rework is something that no company wants to deal with. But they need to. Managing rework brings multiple benefits to the organization, including a smoother supply chain, consistent quality products, and much more. Managing rework and associated responsibilities may be too much to handle, so implementing a quality management system is a wise choice.
A quality management system helps companies tackle errors and problems more efficiently while saving time and money.
13. It Leverages Advanced Reporting and Analysis Tools
Reporting and analysis are quite underrated when it comes to leveraging the potential of collected data. A thorough analysis of trends helps you understand what’s working and what’s not to take the business decisions accordingly. Through reporting, you can share the analysis, trend behaviors, action plan(s), and many other things to the involved parties in a simplified manner.
The next-generation quality management system comes with advanced reporting and analysis tools to help make informed decisions, reduce rework and other overhead expenses.
All the points mentioned above outline that a quality management system helps to reduce the costs of quality in a compliant, timely, and efficient manner.
The Bottom Line
Organizations are always struggling to figure out the difference between the costs they spend on preventing failures versus the amount they spend on fixing the failures. The traditional ways of reducing quality are no longer efficient. It’s time that organizations adopt the next-generation enterprise quality management software like Qualityze EQMS Suite and reduce the quality costs more efficiently than ever.
With an integrated EQMS software, organizations can build quality of culture and compliance wherein everyone will be responsible for quality at their ends. The production will be more about smiles and lesser stress for everyone. Giving ownership to your workforce will make them more confident while keeping them engaged in the core activities.
Quality management software is indeed a worthy investment for holistic improvements.
If you want to know more about the role of QMS in reducing the costs of quality, you can get in touch with the customer success team of Qualityze, and we will be right there for you.
Share
The Start of Something Amazing.
Request Demo
Products
Industries